VOC Rotary Concentrators: How they work, benefits, cost, and other considerations
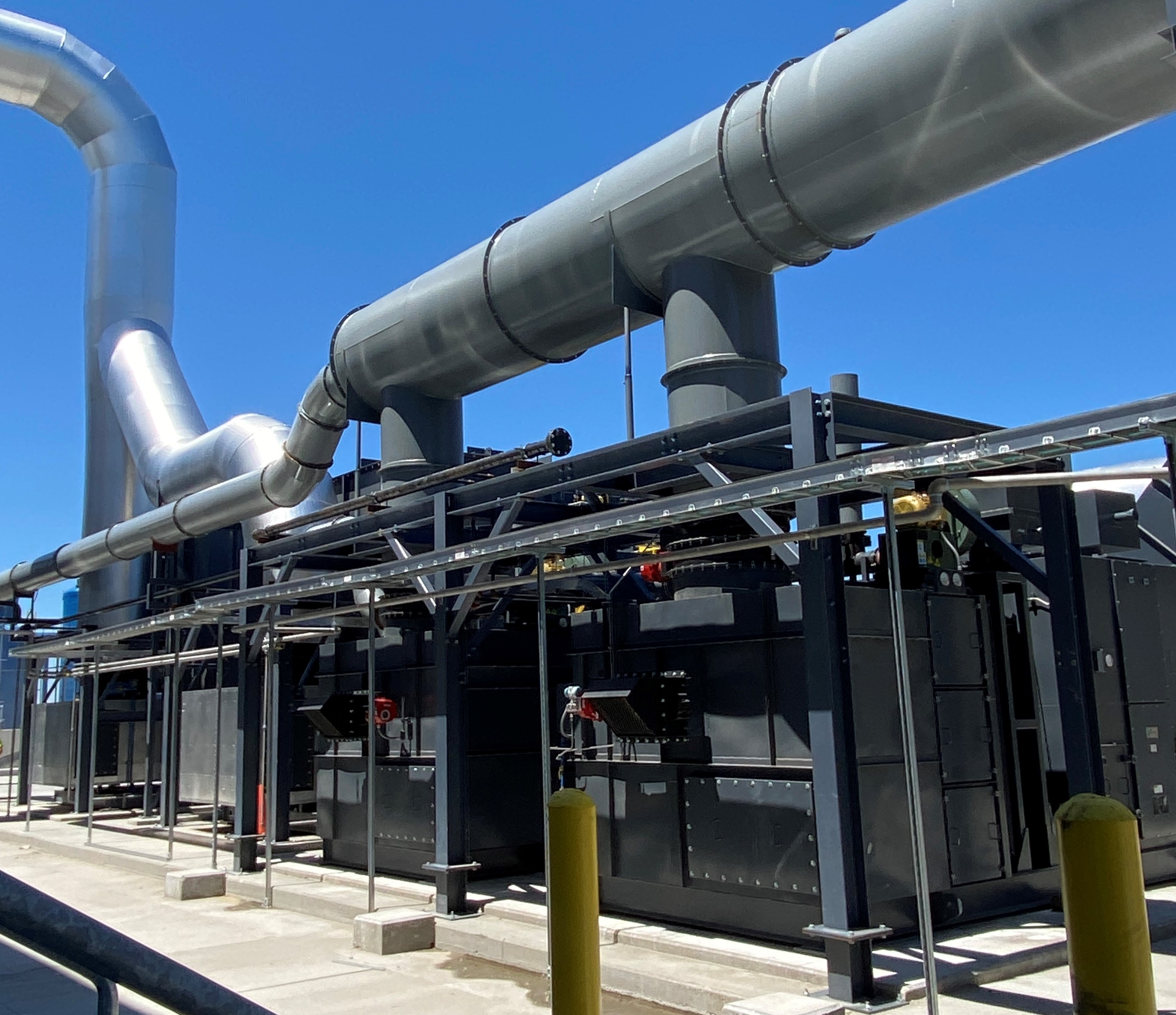
The VOC destruction / removal efficiency (DRE) of a Rotary VOC Concentrator is from 90-97%
A VOC Rotary Concentrator is an add-on air pollution control technology paired with a thermal or catalytic oxidizer. It is a front-end, pre-conditioning unit placed upstream of a thermal, catalytic, or regenerative thermal oxidizer. It is used in applications with a combination of high volume of air with low concentration of solvents. By concentrating the VOCs from a large airstream into a small airstream, it allows the use of a smaller thermal oxidizer (or RTO) and up to 50% utility savings vs. an RTO alone.
Efficiency of VOC Rotary Concentrators
The VOC destruction / removal efficiency (DRE) of a Rotary VOC Concentrator is from 90-97% and is dependent on several factors:
- Type and concentration of VOC
- Process exhaust temperature
- Humidity
How does a VOC Rotary Concentrator Work?
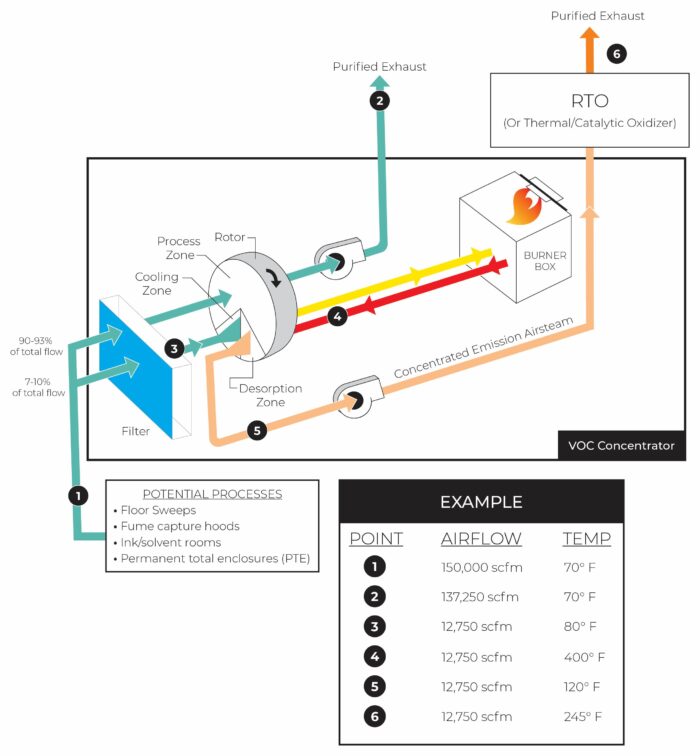
VOC Rotary Concentrators absorb VOCs from a high volume airstream, and release the VOCs to a low volume airstream, that then gets treated in a thermal oxidizer. VOC Rotary Concentrators utilize a honeycomb wheel coated with adsorbent material (typically zeolite) to capture VOCs. This wheel is divided into three sectors: adsorption, desorption and cooling.
Part 1: The Adsorption / Process Zone Section
The process air (1) is split, with 90-93% of it passed through the rotor’s process zone (absorption section) (2) where VOCs are absorbed onto the rotor. The air exiting this section is clean – having given up 98%+ of the VOCs in the airstream to the zeolite rotor – and passes to atmosphere. The adsorption section is approximately 80% of the rotor’s face area.
Part 2: The Desorption Section
This is where the concentrated VOCs are driven off of the rotor. Here a smaller airstream (3) is heated in the burner box (or a heat exchanger) and this hot air (4) is then passed through the rotor to drive off (desorb) the VOCs from the rotor. This air flow now carries the VOCs that were driven off of the rotor surface (5). This small airflow is sent to a thermal, catalytic or regenerative thermal oxidizer for VOC destruction. This small airstream is 7-10% of original process airflow, and is concentrated 10X-15X higher than the original process VOC concentration. The desorption section makes up about 8% of the rotor’s face area.
Alternate Explanation
From point 1 to 2, the air passes through the wheel, gets cleaned and exits to atmosphere. The wheel is made of zeolite, which absorbs certain compounds. If those compounds were not removed, eventually the wheel would become saturated, and any additional VOC would pass right through. To keep this from happening, a small section of the wheel has hot air blowing in the opposite direction (point 4 to 5), driving the VOC off the wheel, sending it to the actual control device (5). This desorption stream is typically 1/10 the size of the large stream passing through the wheel. This makes the control device much smaller and more fuel efficient.
Common Process Example
- Incoming airstream: 150,000 scfm of spray booth emissions; 300 ppmv MEK & MIBK
- Desorption airstream: 12,750 scfm of air with 2910-3000 ppmv MEK & MIBK
A VOC Concentrator coupled with a 12,750 scfm RTO, can be used rather than a 150,000 scfm RTO
In the Cooling Section, a slip stream of process air (3) is passed through the rotor. The slip stream is about 7-10% of the total process airflow (1). This air cools the rotor in this section, preparing it to re-enter the process zone. The air passing through the rotor picks up heat as it passes through the hot rotor (previously heated in desorption section). The cooling sector makes up about 8% of the rotor’s face area.
Benefits of an Integrated VOC Rotary Concentrator/RTO
- VOC destruction of 90%-98% overall when paired with an RTO
- Similar capital cost to a stand-alone RTO
- 30-66% Fuel savings vs. stand-alone RTO
- 30-45% Electric Savings vs. stand-alone RTO
- Similar footprint to stand-alone RTO
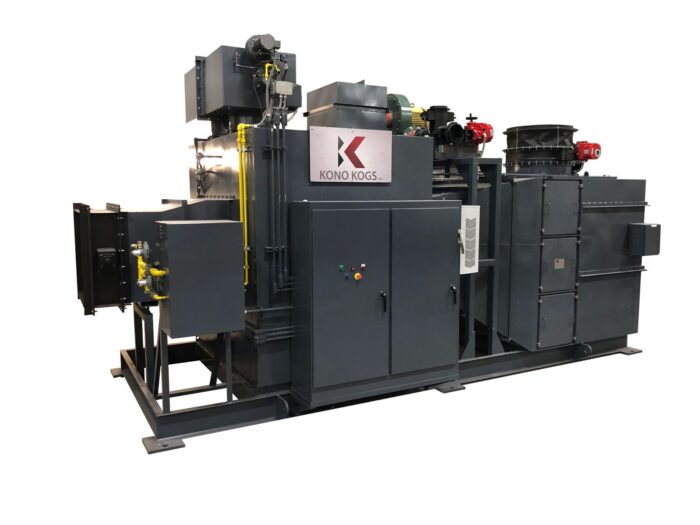
How Much Does a VOC Rotary Concentrator Cost?
Since a VOC rotary concentrator cannot stand alone, the initial capital cost would include the concentrator unit plus a downstream RTO, thermal oxidizer or catalytic oxidizer. The type of oxidizer is dependent upon the application. In addition to the capital cost, the installation plus operating and maintenance cost must be considered. Buying a custom VOC rotary concentrator and a refurbished oxidizer from Kono Kogs can save you 40% or more in capital costs compared to the cost of new, with comparable guarantees and warranties.
Kono Kogs recommends carefully thinking through the Total Cost of Ownership (TCO) before making a purchase. A VOC rotary concentrator and oxidizer system will typically cost more upfront than a stand alone refurbished regenerative thermal oxidizer (RTO) for the same application, but will have a significantly lower operating cost (30-60% fuel savings; 30-45% electric savings). It is important to compare the the total cost of ownership (TCO) of each offering. As a rule of thumb, consider a two-year period when calculating the total cost of ownership (TCO). Send us your application details and we will provide a quick TCO comparing several alternatives including a VOC rotary concentrator/oxidizer system.
Reach out to us for a quote or more information.