Regenerative Thermal Oxidizers (RTO)
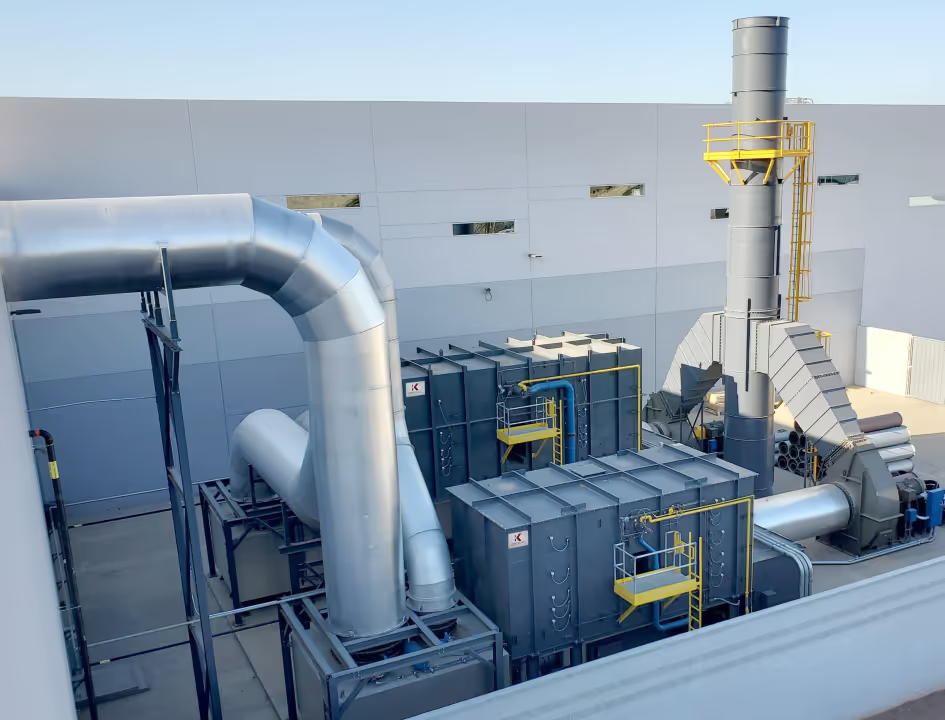
A regenerative thermal oxidizer (RTO) is an air pollution control device that destroys VOCs and hazardous air pollutants (HAPs) in industrial exhaust air. By using regenerative heat recovery, it achieves high fuel efficiency, often operating with 95% heat recovery.
RTO Case Studies
RTO Operation
Maintaining an RTO
Selecting an RTO
FAQs
Induced draft fans are often preferred when handling particulates and solvents with high boiling points, as these solvents can condense and build up on forced draft fan wheels, causing maintenance issues and reduced efficiency.
Using a bake-out feature can help prevent and remove organic compound buildup in the ceramic media, reducing the risk of plugging and maintaining efficient operation. A preheater or recirculatioin loop are also possible mitigation methods.
In most cases, yes. But proper evaluation is recommended to establish that no potential catalyst poisons or masking agents are present in your airstream.
Yes, our RTOs are typically skid-mounted and pre-assembled to minimize field welding and on-site labor. This simplifies installation and helps reduce overall turnkey project costs.
Yes, RTOs can be designed to match your specific exhaust airstream characteristics. They are typically optimized for airstreams with solvent concentrations in the 0–10% Lower Explosive Limit (LEL) range. For higher concentrations up to 25% LEL, additional features such as hot gas bypass systems may be needed to ensure safe and efficient operation.