Thermal Oxidizers (TOX)
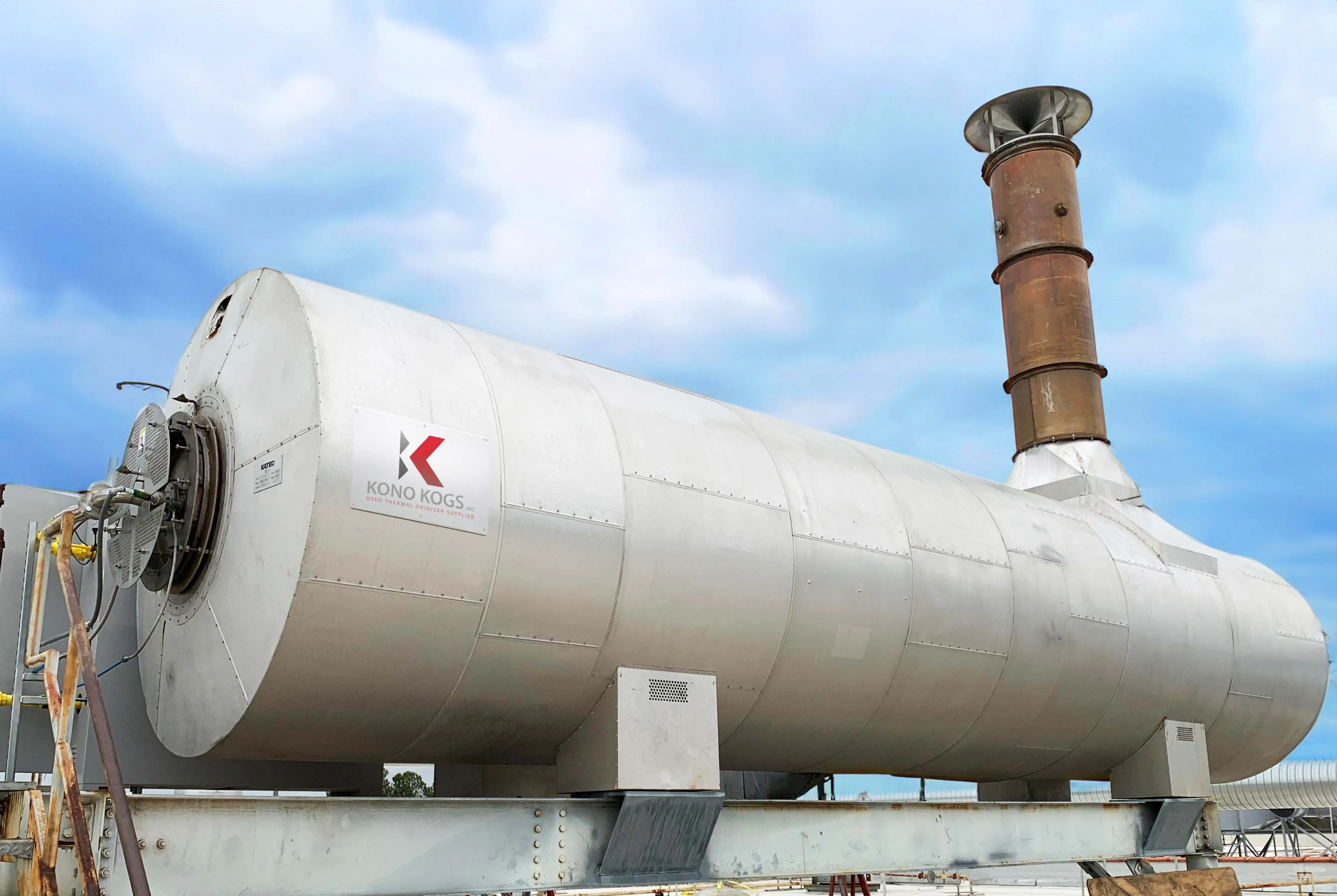
A thermal oxidizer is a combustion system used to control air pollution by destroying hazardous air pollutants (HAPs), VOCs, and odorous emissions from industrial processes. It oxidizes these pollutants at high temperatures, converting them into CO2 and H2O before releasing the clean air into the atmosphere.
Incorporate a Thermal Oxidizer into your emission control strategy to effectively destroy hazardous air pollutants (HAPs) and VOCs. Choose refurbished and save up to 40% or more in capital costs.
TOX Case Studies
All Case Studies
north_east
TOX Resources
All Resources
north_east