How Regenerative Thermal Oxidizers Work
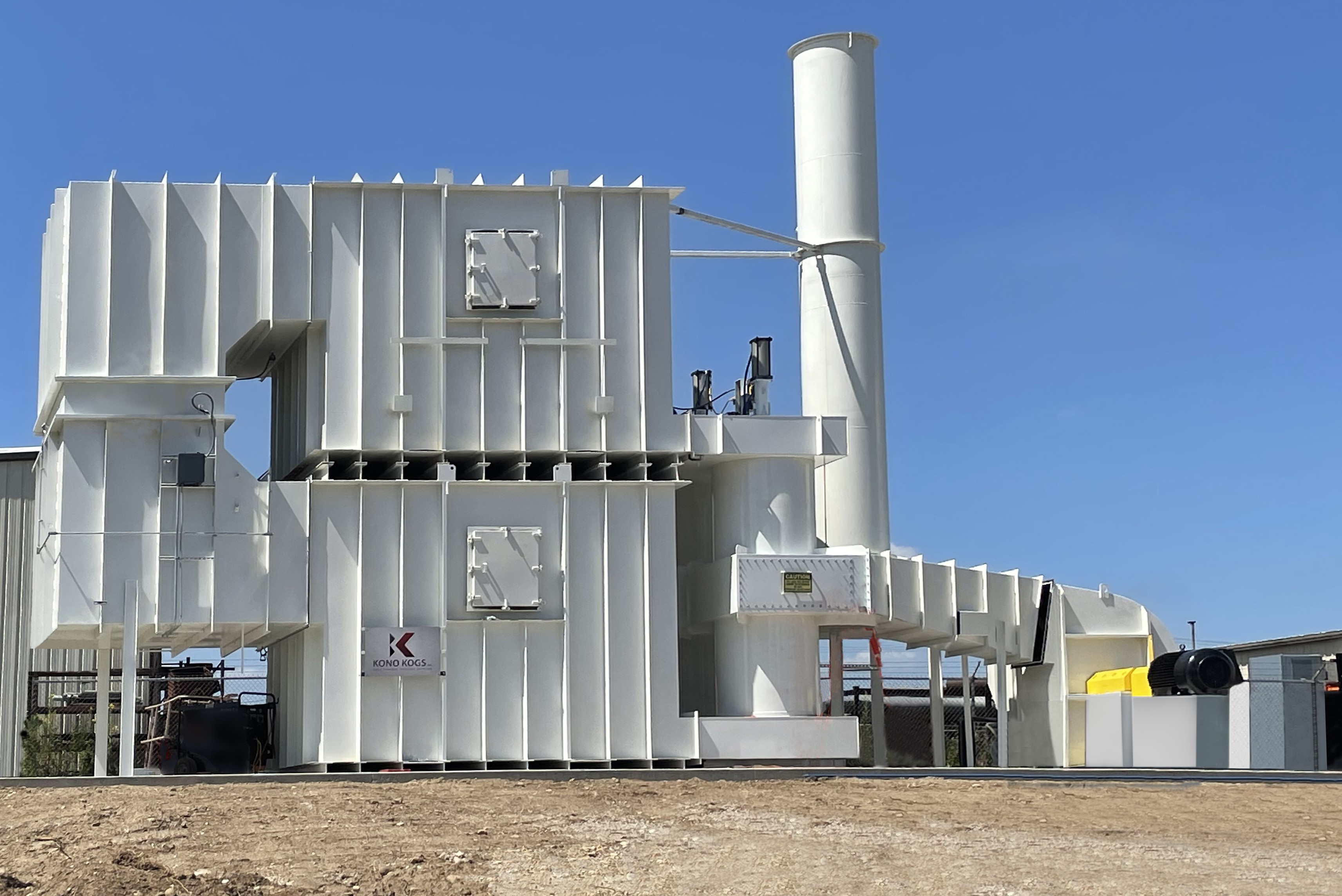
Learn more about how Regenerative Thermal Oxidizers function
The Basics: Regenerative thermal oxidizers heat up the exhaust of industrial processes to "burn off" various air pollutants before releasing it into the atmosphere. RTOs use elements with low thermal conductivity (often ceramic) to preheat the incoming exhaust, which saves on the fuel used to oxidize the pollutants. Heated, cleaned air is then forced through a second set of cooler elements, which cools the exiting air as it's released.
Regenerative Thermal Oxidizer Process Explained
A regenerative thermal oxidizer (RTO) heats polluted industrial exhaust to 1500 – 1600 degrees Fahrenheit to oxidize volatile organic compounds (VOCs) and hazardous air pollutants (HAPs) into carbon dioxide and water vapor. The resulting clean airstream is then released into the atmosphere. The main stages of an RTO process include:
- Pre-heating incoming polluted air
- Combustion and oxidation of polluted air
- Cooling of clean air
- Exhausting of clean air
- Recycling captured heat in order to preheat incoming polluted air
The RTO Difference: Efficiency Through Regenerative Heat Exchange
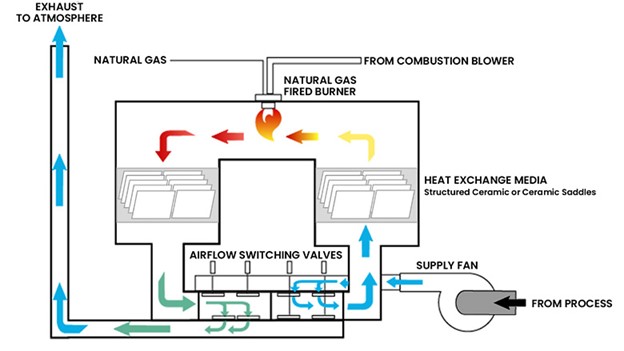
What differentiates regenerative thermal oxidizers from other thermal oxidizer types? It is the regenerative heat exchange process. The defining characteristic of an RTO system is its ability to capture and release heat generated in the RTO oxidation process and “regenerate” this heat to preheat incoming air. This method of heat transfer in a regenerative thermal oxidizer provides exceptional thermal efficiencies. The RTO captures and releases heat from two or more “heat sinks” made up of ceramic media stored in “beds”. The polluted air and the clean air pass through these beds alternately giving off (or absorbing) heat in repeated cycles. Sounds complicated, but it is quite simple in operation.
RTO Preheating through Structured Ceramic Media
To enable this heat retention, the regenerative oxidation process incorporates ceramic media as a heat “sink” to store and then give off heat. These heat sinks are called “beds” in an RTO. The beds are filled with ceramic media material that has been found to be the best heat sink material due to its excellent thermal conductivity, low thermal expansion and shock properties.
Heat Regeneration Cycle: Heat, combust, cool, exhaust. Reverse & repeat
To destroy VOCs and HAPs in process emission airstreams the air is raised to 1600F to oxidize the VOC/HAPs into carbon dioxide and water vapor. Regenerative thermal oxidizers (RTOs) utilize a regenerative heat exchanger that directs the process emissions through a a bed of ceramic heat-exchange media (bed #1) and into the combustion chamber where the pollutants oxidize at high temperature (1600oF). The now hot, cleaned air passes through a second bed of ceramic heat exchange media (bed #2) which absorbs heat, cooling the air before it is finally exhausted into the atmosphere.
Flow Reversal and Heat Exchanger Role Reversal
After a few minutes the airflow direction through the RTO is reversed with a series of opposing valves (or a rotary valve). Heat stored in the ceramic media in bed #2 from the previous cycle is now utilized to give off heat to the polluted airstream that will enter this bed. As the polluted air passes through bed #2, it absorbs heat from the ceramic media; the air rises in temperature, while the ceramic bed is cooled as it gives off heat. The preheated, but still polluted air, exits bed #2 and passes into the combustion chamber. Held at high temperature in the combustion chamber the pollutants in the airstream are oxidized. The now hot, cleaned air passes through a second bed (bed #1 in this cycle) of ceramic heat exchange media which absorbs and stores much of the heat from the air, cooling it before it’s exhausted into the atmosphere as CO2 and water vapor in air.
Reversing the air flow direction optimizes the regenerative heat exchange process to achieve the maximum thermal efficiency, while also achieving high VOC destruction.
Video: Regenerative Thermal Oxidation Process in Detail
Learn more about the RTO thermal oxidation process in this video explained by the thermal oxidation specialists at Kono Kogs:
The RTO Process: Step-by-Step VOC and HAP Destruction
- A system fan draws a pollutant-laden (dirty) airstream from an industrial process and pushes the air through the oxidizer system.
- Airflow through the system is controlled by a rotary valve (in this example; or poppet valves), directing the dirty air into one of two heat exchangers (chambers containing ceramic media beds).
- As dirty air passes through the first media bed, the air absorbs heat from the hot ceramic media, then enters the combustion chamber.
- In the combustion chamber, the dirty air is held at temperature (usually greater than 1500°F) for a specific dwell time (usually > 0.5 seconds). This oxidizes VOCs and HAPs into CO2 and H2O.
- Hot, clean air exits the combustion chamber, then passes through the second ceramic media bed which absorbs/stores the heat from the air, cooling the outgoing clean air.
- Cooled, clean air is then exhausted out of the exhaust stack and into the atmosphere.
- FLOW REVERSAL: The RTO valve changes position every few minutes, reversing the flow direction and alternating heat transfer between the two ceramic media beds.
- This flow reversal gives RTOs their high fuel efficiency and low operating costs, making them highly desirable VOC abatement systems.
Why Regenerative Thermal Oxidation?
Compared to other oxidizer technologies, regenerative thermal oxidizers incorporate a repeated flow direction reversal to achieve exceptionally high performance (VOC destruction & thermal efficiency) while using minimal fuel to keep the system at setpoint temperature for pollutant oxidation. This technique achieves the highest reliability and longest life of all thermal oxidizer technologies.
Find Out More from VOC Oxidizer Specialists at Kono Kogs Inc.
KKI is the leading global supplier of high-quality used RTOs and other air pollution control equipment. Our team has a 100% success rate meeting our performance guarantees and has consistently earned repeat business from our small to our Fortune 100 customers. Whether you’re looking to get more efficient service out of your existing RTO or learn about your replacement options, KKI can help.
Request a quote online or call 920-432-2699 for more information.
Regenerative Thermal Oxidizer Treating Chemical Process Emissions
Case study: Batch chemical manufacturer required emission controls for a process expansion. We supplied a used RTO from our inventory with all necessary features.
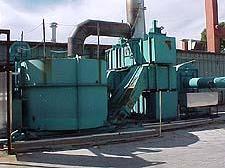
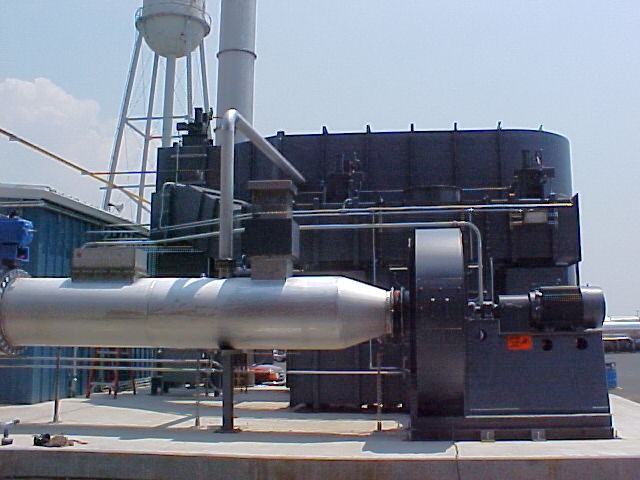