Ceramic Media Replacement in RTOs
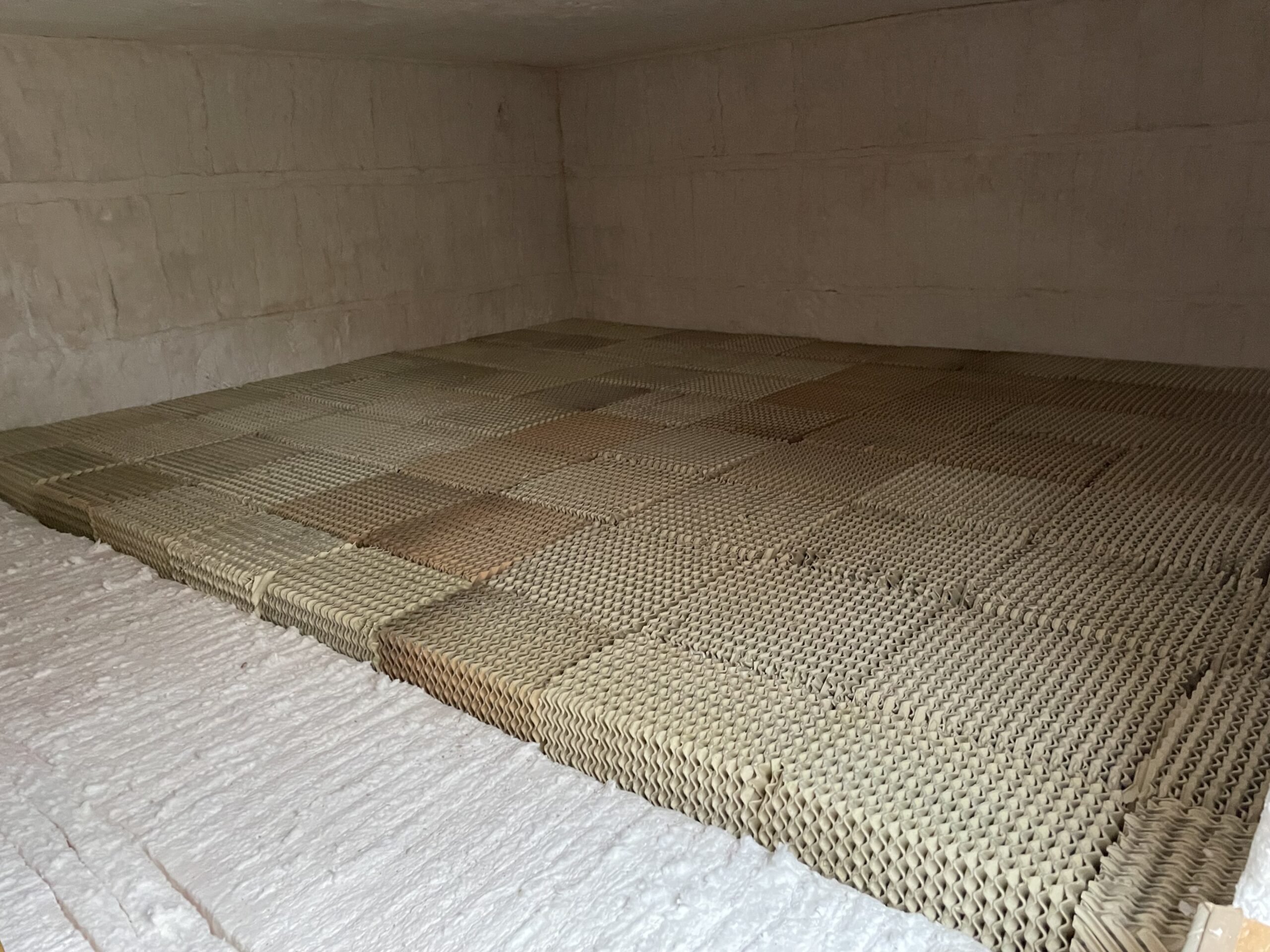
Optimize the Life & Efficiency of Your RTO Ceramic Media Beds
Regenerative thermal oxidizers (RTO’s) have been a workhorse oxidizer for over 30 years. Many ceramic media types and designs have been developed over that time that offer significant improvement in performance and plugging resistance allowing an RTO to be utilized to treat nearly any airstream. Considering ceramic media replacement in your RTO? Wondering about the many options and claims you hear out there? Kono Kogs will offer some clarity for your next step.
Done right, ceramic media replacement offers an opportunity to reduce your current operating costs and future replacement costs. So where do you start?... by knowing your airstream, your RTO, and the signs that your ceramic media plugging are telling you. Organic and inorganic particulates in the airstream present difficult challenges for ceramic media beds. Also, VOC concentration can drive media selection in some cases. Your RTO’s air flow characteristics can also expand or limit your ceramic media options.
Contact the Kono Kogs team for a free analysis, or learn more below.
Commonly asked questions about Ceramic Media Beds
Yes, the type of ceramic media in an RTO can be optimized for an exhaust airstream. Using the right type of ceramic media can maximize thermal efficiency, minimize pressure drop, and better handle organic and inorganic particulates that may be present. Check out this case study for more information.
Note: Regular preventative maintenance and understanding your airstream's composition are cruical for determining the appropriate timing for media replacement.
Know Your Airstream
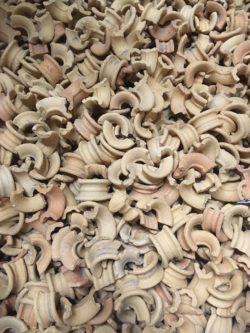
Particulates: Particulate (dust/sticky VOCs/silicones) can really shorten the life of a ceramic media bed. Particulates not known- or not planned for-will usually get caught up in the ceramic media bed. This can be a costly surprise for a new RTO owner-sometimes requiring bed replacement in the first few years of ownership. Knowing the volume and characteristics of particulates in your airstream is the first step to designing the best ceramic media bed for your application.
A ceramic media bed is a very good filter, but that is not its purpose! With proper understanding of the airstream, a ceramic media bed can be designed to optimize the heat exchange performance (its true purpose), while allowing particulates to pass through the beds and reduce plugging; extending the life of the RTO bed. There are a wide variety of structured ceramic media choices, with various flow path opening sizes to provide passage of some or all particulates.
Or if particulates can’t be completely mitigated but only reduced- the RTO may benefit from a design that “captures” particulates in the top layer of the bed, limiting the scope of future replacement to the top layer only; with the goal to make future replacement quicker and less costly.
If particulate buildup is unpredictable and affects the entire volume, a better bed selection might be one that is easy and less costly to replace- in terms of capital cost and required downtime- while still achieving thermal efficiency. The lowest cost option is usually random packed ceramic media, like saddles. Basically, plan for the inevitable buildup and accept that there will be frequent, but less costly, replacement.
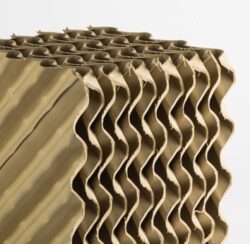
VOC Concentration: Volatile organic compound (VOC) concentration can determine the flexibility available when selecting ceramic media. Since fuel costs are typically the largest operating cost contributor for an RTO, the first goal is to provide the highest thermal efficiency possible for the lowest capital cost. That would be the simple approach if the airstream is without particulate and the RTO design has good flow characteristics. The media bed design then comes down to economics only: optimal thermal efficiency vs. bed replacement cost.
However, if the VOC concentration is high and particulates are present, the media bed can be de-rated in thermal efficiency to accommodate expected plugging, but still have no negative impact on fuel costs. This de-rating can be done by reducing the depth of the ceramic media bed, or by utilizing structured media with extra-large flow paths.
Know Your RTO
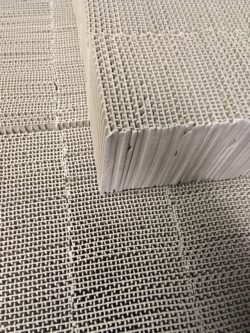
RTO Airflow: We have handled nearly every RTO model on the market. Some have well designed airflow mixing. Others, by limits of their design, do not properly distribute the airflow before entering the beds. This is a problem if structured ceramic media is being considered. Structured beds have shallow depth, and typically maintain any flow imbalance all the way through the bed, with no lateral (side to side) mixing of air volume. This unbalanced flow in the beds reduces the thermal efficiency of the bed. Also, unbalanced flow through the beds can reduce the VOC destruction performance of the RTO due to poor temperature distribution (cold pockets).
How is unbalanced flow corrected by the design of a ceramic media bed?
By creating flow resistance (pressure drop) through the bed we can create better flow distribution before the air enters the bed. We can also use media that encourages mixing in the lower, entering layer. Different styles of ceramic media (saddles or structured) produce differing resistance as air passes through the bed.
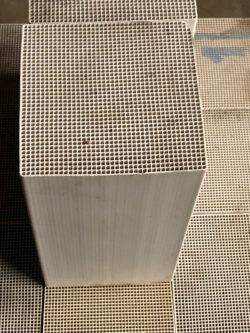
By selecting ceramic media mixes that create an optimized pressure drop across the beds we can:
- Correct the intrinsic flow imbalance of an RTO system.
- Optimize the thermal efficiency and the VOC destruction efficiency for a specific application.
Choosing 100% random media would provide the best flow balancing if that were the main goal, but that choice may create an unnecessary pressure drop and an increased fan horsepower draw. Usually a mixed bed of random media + structured media or a mix of several structured media types will be the best option.
Bonus: Can the Flow Capacity be Increased?
Usually, yes. New structured media design advances can improve older beds, providing as much as 25% capacity increases over beds that utilize saddle ceramic media. Fan and burner capacity studies will be needed to determine the actual airflow increase possible.
Signs of Ceramic Media Plugging in Your RTO
Ceramic media beds in RTOs have extremely long life (10-20 years) when not exposed to adverse operating conditions. But some applications have these adverse conditions, and they can greatly impact the performance of an RTO, including the life of the ceramic media bed. One of the most common causes of ceramic media replacement in a regenerative thermal oxidizer is plugging of the ceramic media beds. There are many causes of ceramic media plugging (blockage) and, unfortunately, some can only be addressed with a full replacement of the ceramic media bed.
Most plugging can be seen with a simple visual inspection during scheduled preventive maintenance. But until the downtime is available for an inspection, here are some common signs of media bed plugging.
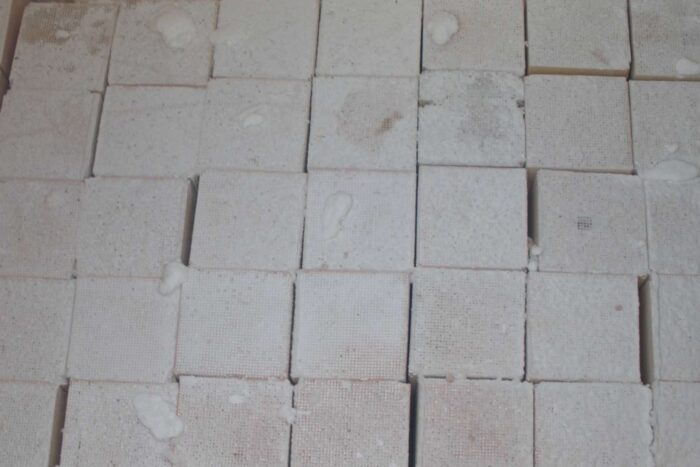
Signs of Ceramic Media Plugging in an RTO include:
- Process/emission source performance issues:
- Poor drying performance in an oven
- Increased odor at the process
- Spray booth: Poor product quality from over spray evacuation
- Increased pressure pulse from RTO back to the oven/process
- Tripping of pressure switch at the emission source (oven, paint booth, etc.)
- Pressure pulses in the building
- Reduced air flow capacity through the RTO
- Increasing variable speed drive amperage (frequency) for the same operating conditions
- Increasing fuel consumption
- Tripping of pressure switches during poppet valve actuation (RTO and at the process)
- Oil-canning of the ceramic media bed walls during valve switching (in extreme cases)
Organic build-up that leads to plugging is the most common cause of plugging and typically can be treated with a bake-out feature. To address inorganic build-up, wash-outs (water + chemical) are an option to buy more time. However, in the majority of cases plugging due to inorganic material will eventually require replacement of the ceramic media bed.
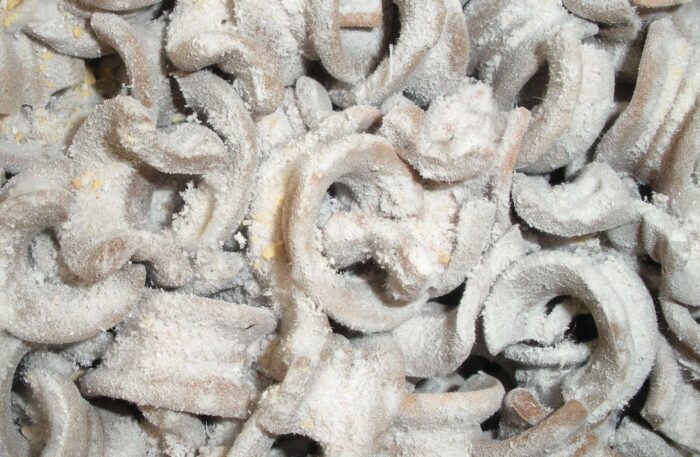
Sources of Inorganic Plugging in an RTO:
- Paint solids
- Silicone release coatings
- Semi-conductor fabrication (Hexamethyl disilizane; HMDS)
- Siloxanes
Regular RTO preventive maintenance (PM) can identify potential plugging concerns. Being proactive with PM will allow you to plan for treatment or replacement of the ceramic media before the problem causes the plugging symptoms described above. Contact us for guidance if plugging is experienced in your system. We can help you assess the source and develop a plan to address the ceramic media plugging in your RTO.
Ceramic Media Replacement Case Studies
To see examples of our work including plenty of photos, check out our case study involving ceramic media replacement.
Summary
The RTO and your application introduce many variables affecting ceramic media selection and each variable is co-dependent upon the other. Fortunately, there are options available to optimize airflow mixing, increase thermal efficiency, and mitigate fouling. So, for the next ceramic media replacement in your regenerative thermal oxidizer make it a point to know your airstream, and know your RTO. This will lead to a successful ceramic media bed replacement in your RTO.
Ceramic media replacement does not have to be a mystery. We have seen just about everything and offer free analysis and guidance. Send us your unique application and we will prepare a quote quickly including removal and replacement of your existing ceramic media bed.
Contact Kono Kogs with questions or request a quote for ceramic media replacement
RTO Cold Face Repair and Ceramic Media Replacement
Case Study: We repaired the cold face support & replaced the ceramic media in mothballed RTO to provide additional capacity for our client's plant expansion.
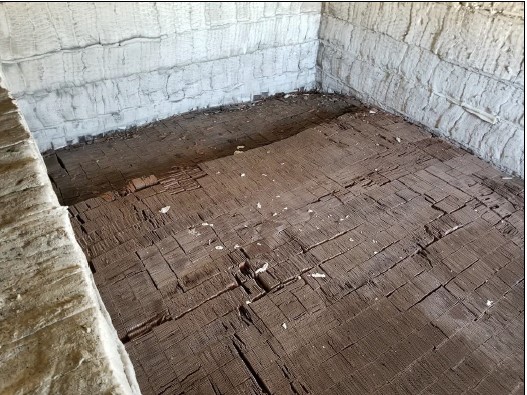
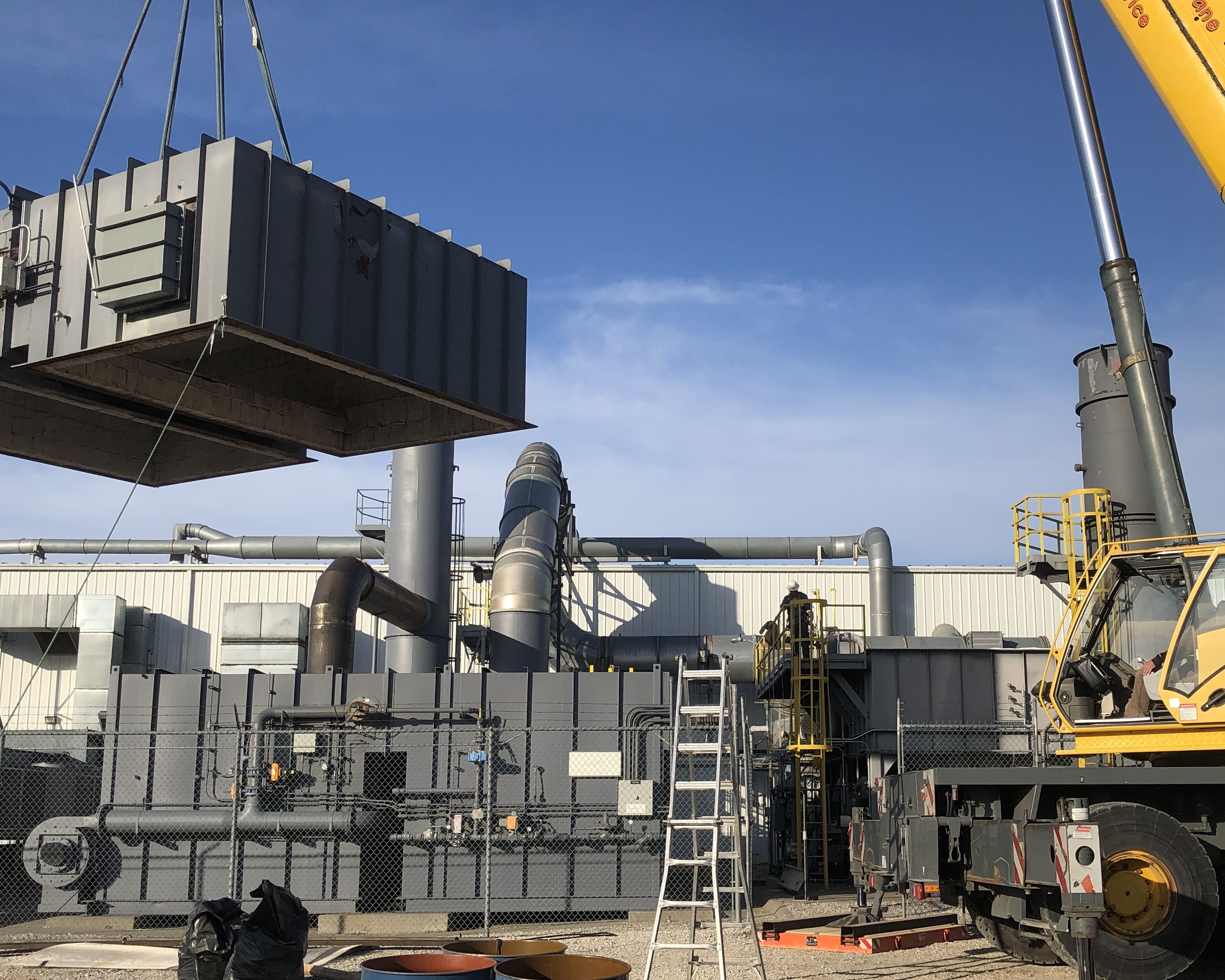