RTO w/VOC Concentrator Treating Metal Decorating Emissions
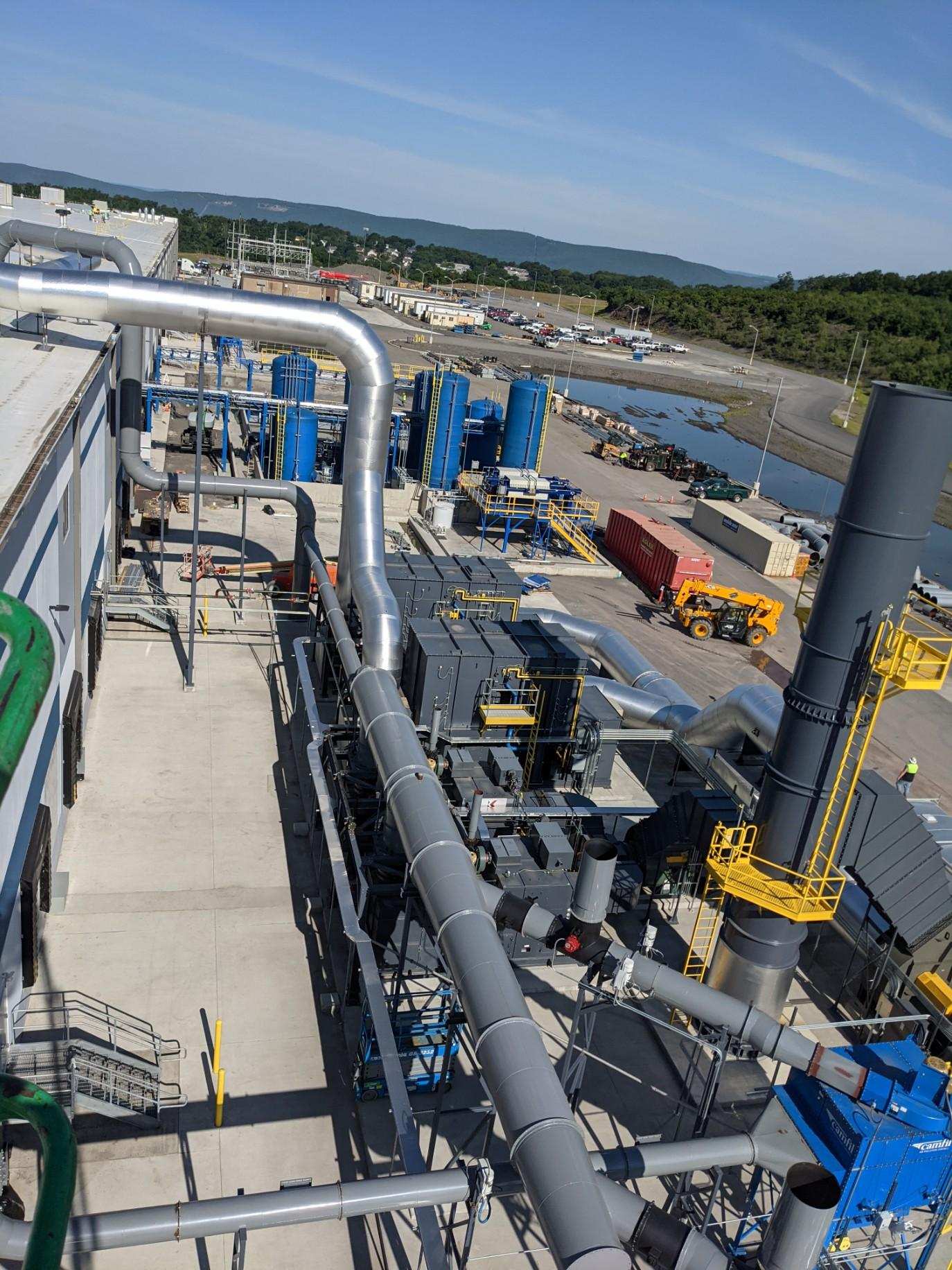
Emissions at a new can making facility are being treated by a refurbished RTO/VOC concentrator system. The system consists of 2 refurbished RTOs and 3 VOC concentrators, all providing high VOC destruction and very low gas and electric powrer demand.
Problem
A metal decorating (can coating) operation needed emission control for a new facility with multiple can coating lines. The emissions included two significantly different airstreams varying in both temperature and Volatile Organic Compounds (VOCs) concentration. Historically this process was treated by sending both airstreams to a single regenerative thermal oxidizer (RTO), and when needed, included a pre-heat section. The pre-heat section prevented condensation of VOCs in both the incoming ductwork and at the RTO inlet caused by mixing hot & cold airstreams typical to can coating lines. To prevent condensation, the incoming air was heated in the pre-heat section with an auxiliary burner (See related case study here for more information) to keep it above condensation temperature. This approach worked well but was costly due to the high fuel demand of the pre-heat section.
Photos: In Progess
Click on a picture to enlarge
Solution
Kono Kogs offered an innovative approach utilizing VOC concentrator technology paired with our refurbished RTO systems. This integrated system solves both the air mixing problem, and significantly reduces the fuel use typical with a stand-alone RTO and a pre-heat section. The design keeps the two differing temperature airstreams segregated, eliminating condensation concerns, and also reducing the fuel use typical with a pre-heat box. In this system the cool, low VOC concentration airstream from the decorators, inside spray machines, and conveyors is routed through the VOC concentrator, and the resulting hot concentrated airstream from the VOC concentrator is sent to the RTO for final VOC destruction (see What is a VOC Concentrator? for more details). The pin oven and inside bake oven exhaust are routed directly to the RTO for treatment, and combined with the concentrated, warm airstream from the VOC concentrator. The combined airstream is routed to the RTOs for final VOC destruction.
What would have been treated by an 80,000 scfm RTO with a pre-heat section, now is treated by an integrated VOC Concentrator + RTO achieving a 60% fuel savings, 40% electric savings, and a similar physical footprint.
Equipment & Services Provided
- Fully refurbished Durr MEGTEC Clean Switch RTOs
- New VOC Rotary Concentrators li>Mechanical assembly of RTO & Concentrator
- Fab & install process ductwork & T-dampers
- Equipment and crew to install RTO and ductwork
- Equipment commissioning
- Parts Warranty & VOC destruction warranty
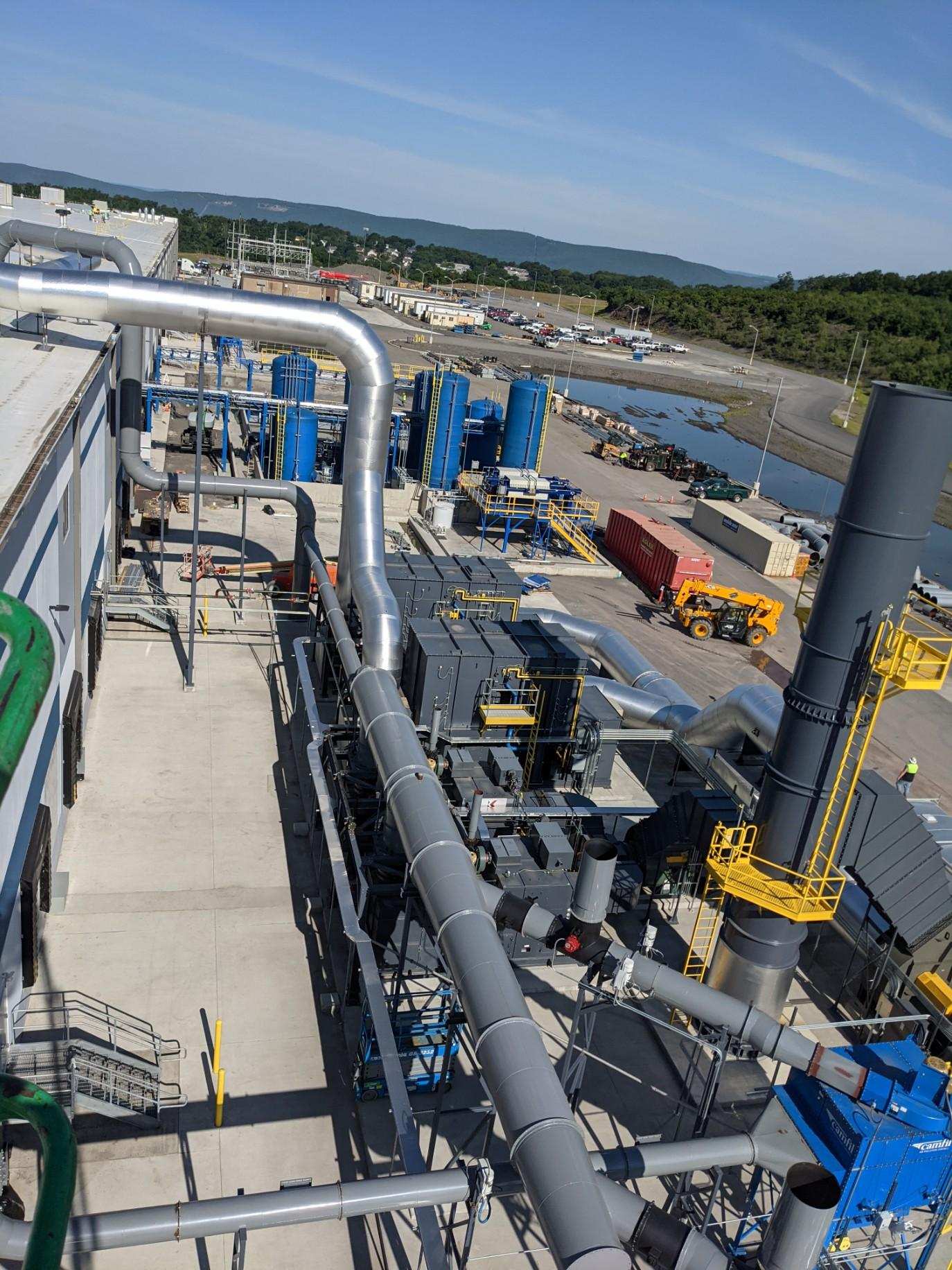
Envision it and our team can get you there
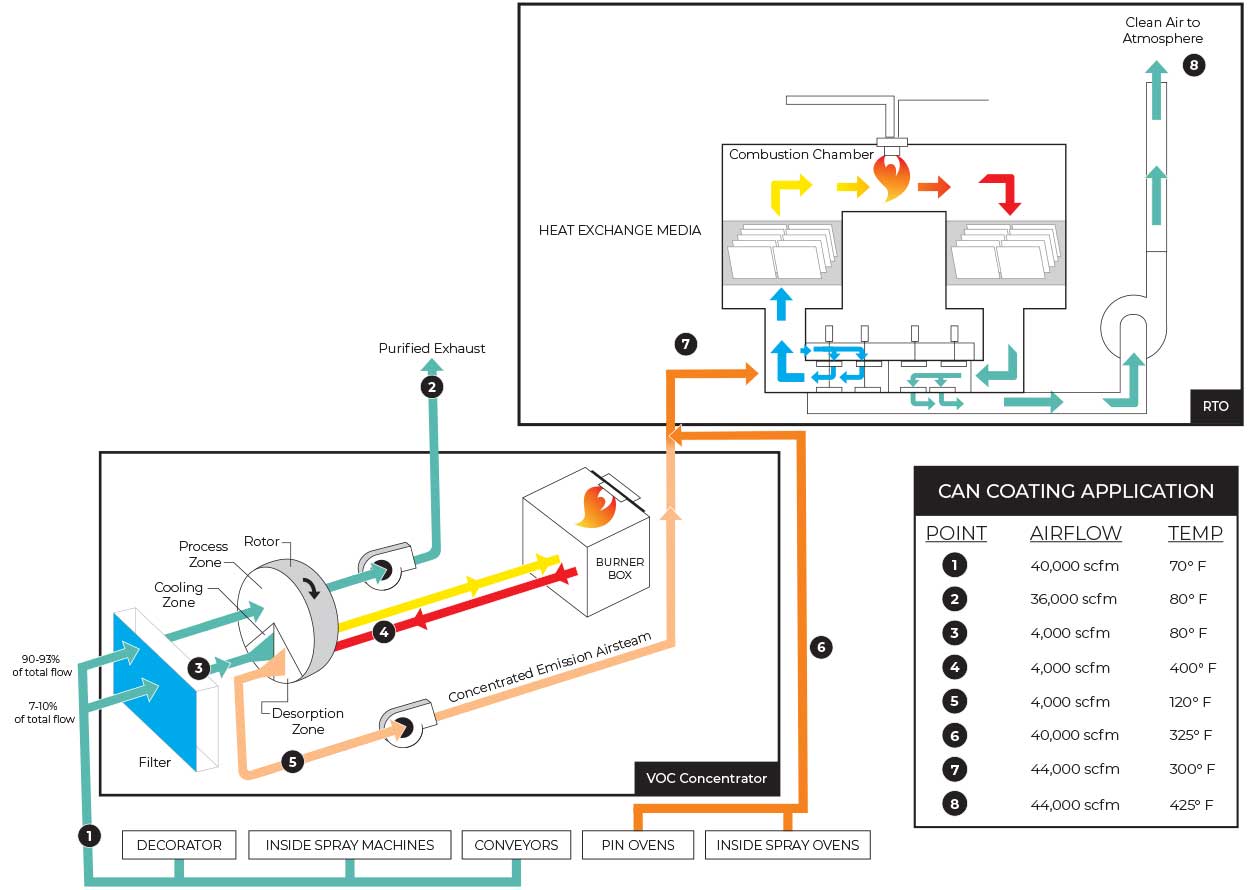
Kono Kogs – A Proven Solution Provider for Emission Control Projects
Kono Kogs fabricated and installed the VOC concentrators (3), refurbished the RTOs (2), fabricated and installed all ductwork, dampers and support structure, provided wiring, piping, and equipment commissioning- even installing our customer's other purchased equipment. We can't do it all, but we can do much, and strive to do it very well.
Call Us: From Full Turnkey Projects to Simple Thermal Oxidizer Maintenance
Our team of industrial oxidizer experts handle everything related to regenerative thermal oxidizers including emergency services, field repairs, field rebuilds/upgrades, preventive maintenance service, relocation, trade-in, and replacement with our refurbished, warrantied long-life RTO systems. We have hundreds of refurbished oxidizer units installed worldwide. Contact us to learn more about refurbished oxidizers to satisfy your processes' VOC abatement requirements.