Industrial Oxidizer Advances Worth the Investment
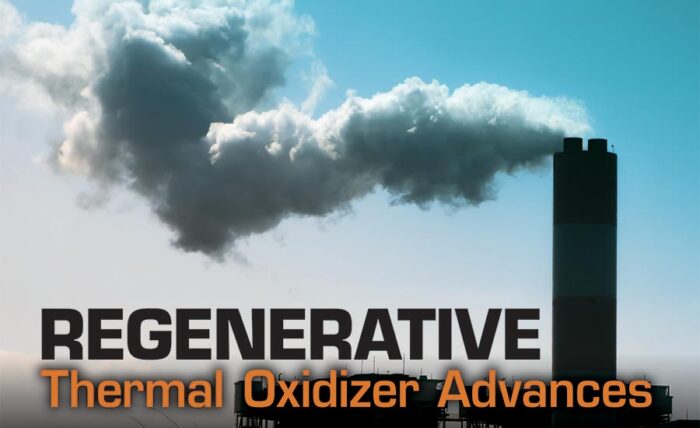
Industrial Oxidizer Tech Developments & Their Benefits
This article will look at industrial oxidizer technology developments and the benefits they provide — both for new oxidizer purchases, and for retrofit on existing regenerative thermal oxidizer systems.
In an article published in the November 2018 issue of Process Heating Magazine we discuss some recent, proven advances seen in regenerative thermal oxidizer technology. Enjoy the article below, and call us with any questions.
Regenerative thermal oxidizers (RTO) came on the scene some 35 years ago and, for the past two decades, have been the “technology of choice” for industrial VOC control. With many incremental improvements, regenerative thermal oxidizers do not risk losing this status any time soon. What innovations have secured the RTO’s role into the foreseeable future, and how can they improve your operation?
To be transparent, this view on oxidizer technology developments originates from the perspective of an oxidizer rebuilder. As new equipment suppliers (OEMs) release oxidizer innovations, the promises on the glossy brochures get put to the test. Rebuilders have the benefit of inspecting an “experienced” regenerative thermal oxidizer with years of operation logged. This allows an objective review of oxidizer technologies by their performance and condition.
Development Timeline for Regenerative Thermal Oxidizers
Before reviewing RTO technology innovations, it might pay to quickly review the history of regenerative thermal oxidizer technology.
At its launch in the 1980s, the regenerative thermal oxidizer offered notable fuel savings compared to its nearest competitor in the oxidizer arena, the thermal recuperative oxidizer. The regenerative thermal oxidizer’s advantages came with one notable offset: a large required investment in capital costs, footprint and assembly. Yet, even with those added costs, regenerative thermal oxidizers were still attractive because the fuel-savings payback was fast. On top of that, the life expectancy of an RTO was significantly greater than thermal recuperative oxidizers. Those units had intrinsic restrictions due to the limits of stainless steel and exotic metals at typical operating temperatures(1400 to 1550°F).
As more run-time experience was gained, RTO suppliers found ways to reduce the capital-cost investment. One technique was by simplifying the ceramic-media support (cold face), shrinking the combustion chamber size and shape, achieving high VOC destruction with only two media beds, and incorporating pneumatically driven poppet valves. Moreover, structured ceramic media became a viable option for most applications, reducing system horsepower output. Modular, bolt-together systems were developed for ease of assembly, and equipment footprints were significantly reduced as switching valves, feeder ductwork and media chambers were packaged in creative ways. Fuel injection came on the scene as well, offering additional fuel savings versus conventional burners. Finally, rotary-switching valves were introduced to address a need for reduced pressure pulses upstream of the oxidizer.
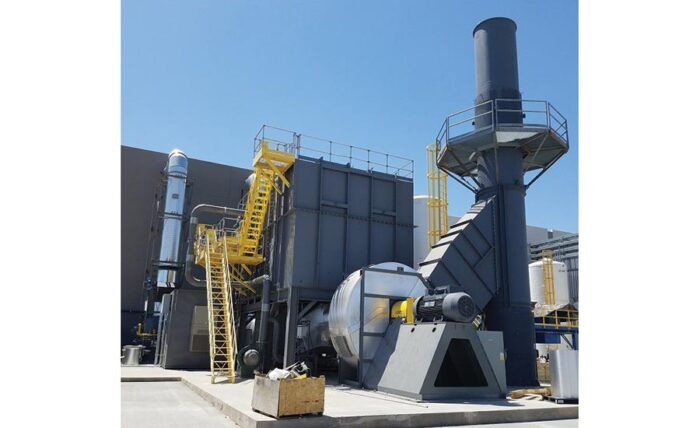
In the 2000s, rotary-switching valve RTOs became more competitive. Designs were developed to treat large flows (greater than 80,000 SCFM) in a single oxidizer. Advances in PLCs continued to simplify RTO troubleshooting, and remote monitoring became commonplace, reducing maintenance costs.
Technology advances over the history of regenerative thermal oxidizers have resulted in options to seek in a RTO or to consider retrofitting on an existing RTO system.
Rotary-Switching Valves
Rotary valve designs have become ubiquitous in recent years. Rotary valve technology switches the airflow direction in a regenerative thermal oxidizer with a single valve. Seal rings and a positive-(or negative-) seal air blower maintain the division of clean and dirty air prior to and during valve switches. This provides several benefits.
Reduced Pressure Pulse Back to the Process. Necessity being the mother of invention, rotary valves solved the pressure-spike problem common to poppet-valve systems. With poppet-valve switches, pressure spikes made their way upstream to the process being treated. Some products were sensitive to changes in pressure, resulting in problems such as web movement, product marking, coating-density variations and falling product within the oven. Rotary valves have succeeded in nearly eliminating the pressure pulse upstream of the RTO.
Smaller Footprint in Large Flow Applications. Rotary-valve RTOs can achieve significantly smaller footprints in flow rates over 20,000 SCFM (figure 1).
Reduced Components, Less Maintenance. Most rotary-valve systems in the field are driven by a single air cylinder and solenoid valve. Contrasted with poppet valves, the components required are cut in half, increasing valve reliability.
Electric-Drive Rotary Valve Eliminates Weather Freezeups. New designs are utilizing variable-speed drives to actuate the rotary valve. This simplifies the drive actuation, setup and tuning. More importantly, it addresses the risk of pneumatic system freezeup if excess moisture exists in the air supply.
Retrofit Potential. Integration into an existing system would be challenging and costly due to connections with the media chambers and ductwork. Such a retrofit would provide little to no operational cost savings.
Mixed Media Beds
Ceramic media is the heart of the regenerative thermal oxidizer. As air passes through the ceramic media, it absorbs or releases heat in the regenerative process, providing exceptional thermal efficiencies. Media manufacturers continue to optimize their offerings to gain better performance with reduced pressure drop and cost. Typical media offerings include random packed and structured types, with a variety of shapes available in both styles of media.
OEMs and rebuilders have recently been customizing individual media layers based on the application needs (figure 2). For example, a clean airstream might use 100 percent structured media; a slightly lower thermal-effectiveness media as a base layer; and top it with the highest thermal-effectiveness media. This combination provides good flow-distribution properties, excellent thermal efficiencies and even air distribution.
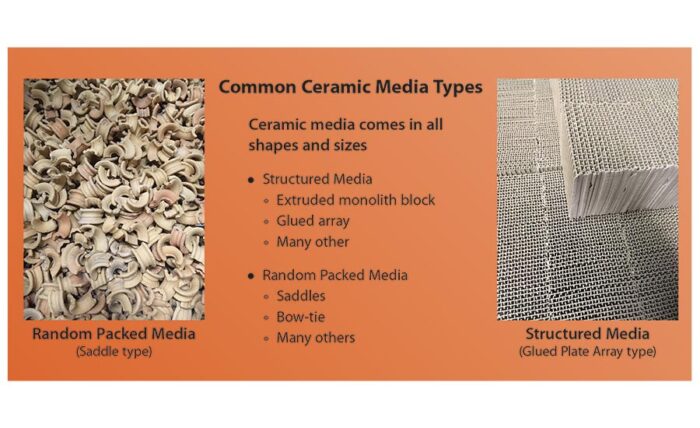
Other applications such as those with the potential for silicone plugging require different media bed layers. It might use a mix that captures silicone buildup on the random media while protecting the underlying structured media, which has smaller flow channels susceptible to plugging. Likewise, a process with particulate may benefit from a different mix.
The possible media mixes are endless, but typical bed mixes consist of two to three ceramic media. Each application benefits from a review of possible mixes with an eye toward optimizing thermal efficiency while extending bed life or simplifying bed maintenance.
Retrofit Potential: Excellent. Ceramic media replacement with a custom mix pays for itself in fuel and electric power savings. Some options provide exceptional payback periods.
Fuel/Air Ratio Control Systems
Advances in fuel/air ratio control systems can help an efficient RTO become even more fuel efficient. Burner manufacturers have been offering fuel/air ratio control systems for more than a decade. These systems incorporate special valves, flowmeters and computer controls to monitor and control fuel and air mass ratios to optimize fuel burning.
Incorporating a fuel/air ratio control system on a conventional gas train is similar to replacing a carburetor with a fuel-injection system. OEMs can provide a payback analysis for this optional feature. Payback timing is based on the expected emission stream. Payback is quickest on high flow, low VOC concentration applications like paint spray-booth emissions.
Retrofit Potential: Excellent. Some ratio control systems can be elaborate to retrofit. Others require only a few component changes within the existing gas train.
Remote Monitoring/Troubleshooting
New communication technology allows remote monitoring and connectivity with an RTO’s PLC from a computer or device — located next door or hundreds of miles away. What was originally accomplished with a phone modem has matured to fast, secure virtual private network access. VPNs enable access to the oxidizer’s PLC, drives, human-machine interface (HMI) devices, and any other device connected to the machine subnet. This allows review of temperatures, pressures, fan speeds and subsystem performance to quickly identify problems. Remote access can reduce travel costs and downtime. The data is delivered in real time and can help troubleshoot an equipment issue. Also, scheduled monitoring and trend analysis can identify potential issues before they result in downtime or require technician travel (figure 3).
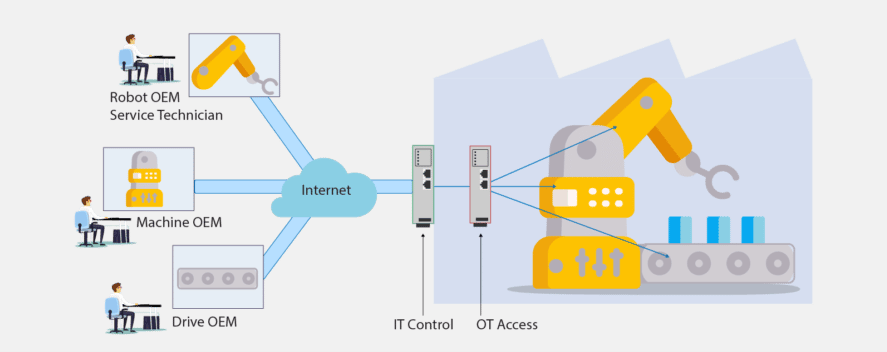
Retrofit Potential: Excellent. Any PLC is a candidate for a remote monitoring with the newest VPN technology.
REMOTE TROUBLEHOOTING SERVICES
In conclusion, these are highlights of recent advances in regenerative thermal oxidizer technology. Each of these options can benefit buyers of new RTO systems, and some may benefit current RTO owners willing to retrofit wisely. For plant managers, engineers and maintenance staff, leading-edge innovations may be intriguing. Proven technologies, however, provide reliable oxidizer performance that frees up plant personnel to focus on other proactive opportunities.
Industrial Oxidizer Specialists
Kono Kogs is the world’s leading supplier of used industrial oxidizer systems. Our core team has 150+ years of combined application and technical experience, and a 100% success rate meeting performance guarantees. We would very much like to help you find an economical solution to your emission control needs through oxidizer repair, upgrade or replacement. We’re happy to provide a free cost-benefit analysis for your application.
Regenerative Thermal Oxidizer Treating Encapsulating Line Emissions
Our refurbished RTO system for an encapsulating company provided low TCO (capital cost, operating cost, maintenance cost) & significant savings over new.
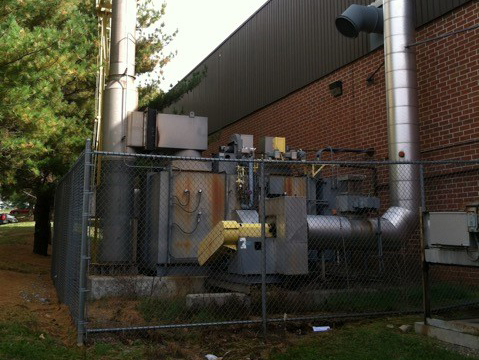
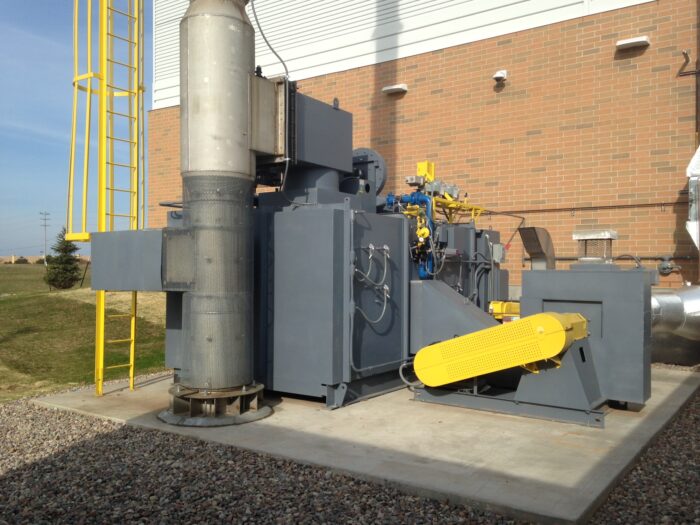