Thermal Oxidizers (TOX): What they are, what they do & more
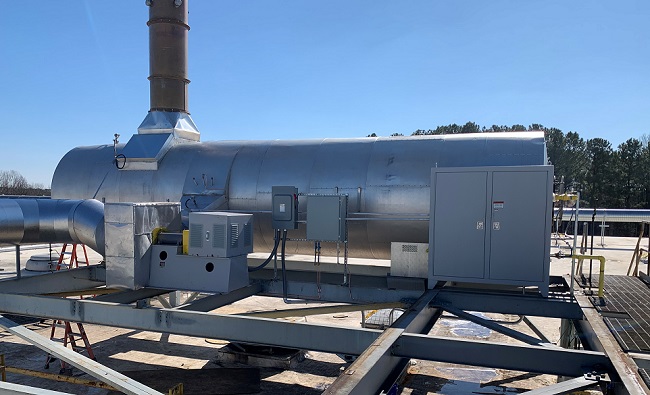
A thermal oxidizer combusts hazardous air pollutants (HAPs) at high temperature for air pollution control.
A thermal oxidizer is a combustion system used to control air pollution by destroying hazardous air pollutants (HAP), volatile organic compounds (VOC), and odorous emissions discharged from industrial processes. Also referred to as TOX or thermal incinerator, a thermal oxidizer is designed to oxidize hydrocarbon-based pollutants into CO2 and H2O before exhausting them to the atmosphere.
TOX Basics
TOX Operating Principles—Thermal oxidizer (TOX) technology collects air emissions from industrial exhaust airstreams containing VOCs and HAPs, raises the airstream to high temperature to oxidize (convert) the pollutants into CO2 and H2O before releasing the clean airstream into the atmosphere. Like other oxidizer systems, time, temperature, and turbulence are the key to proper performance of a TOX.
LEARN MORE - How Thermal Oxidizers Work
Frequently Asked Tox Questions
Thermal Oxidizers (TOX) have a heat recovery (efficiency) of 70% typically, but some custom designs will use lower efficiency heat echangers if VOC concentrations are elevated. This technology has higher operating cost than most oxidizer systems.
TOX with heat exchangers typically have a shorter life span than CATOX systems or RTO systems. This is due to the elevated operating temperatutres that te heat exchanger is exposed to. Especially deterimental to the system are repeated on/off cycling that imposes significant thermal stress on the heat exhanger. It is best to apply these systems in applications that run 24/7/365.
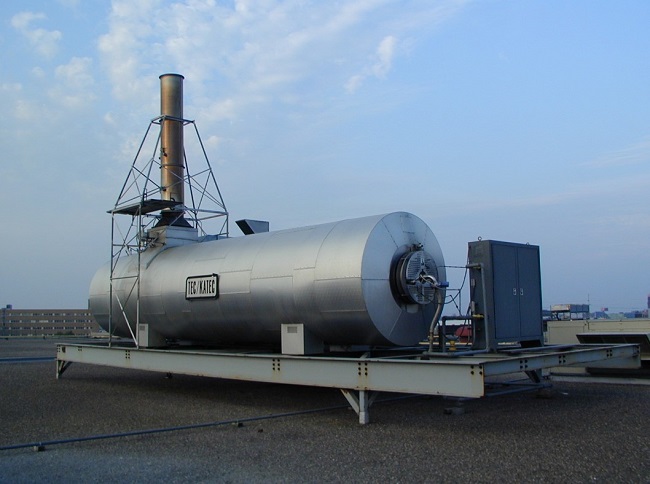
Who Uses Thermal Oxidizers?
Thermal Oxidizers are used by manufacturers in a wide range of industries and applications. The Kono Kogs team has experience with practically every possible oxidizer application across many industries around the globe.
We have an in-depth understanding of every process airstream our systems are used to treat. Explore our thermal oxidizer case studies or contact us with questions about the different technologies available for your specific application.
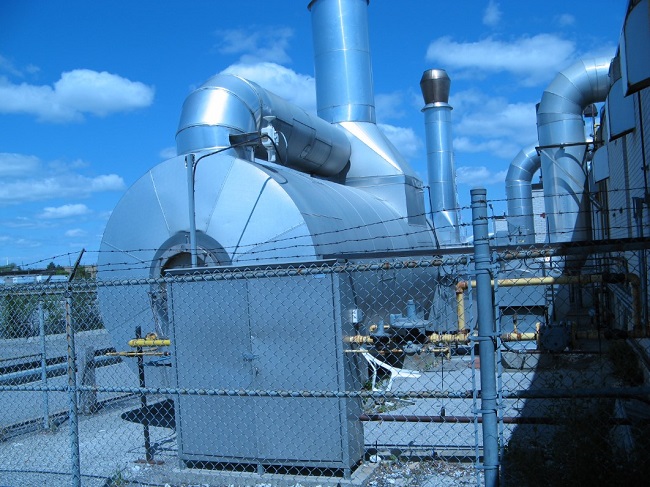
How Much does a Thermal Oxidizer Cost?
The cost of a thermal oxidizer addition includes the initial capital investment in the equipment as well as the operating and installation costs. Buying a pre-owned, fully refurbished thermal oxidizer from Kono Kogs can save you 40% or more in capital costs compared to the cost of new, with comparable guarantees and warranties.
See our Thermal Oxidizer Budget Calculator
Kono Kogs recommends carefully thinking through the Total Cost of Ownership (TCO) before making a purchase. A thermal oxidizer system with a low capital cost might not represent your lowest TCO in operation over time. As a rule of thumb, consider a two-year period when calculating the total cost.
Capital Costs Include:
- Equipment
- Shipping
- Installation
- Commissioning (start-up)
Operating Costs Include:
- Fuel
- Electricity
- Compressed air
- Maintenance service
Both capital and operating costs can vary widely between different thermal oxidizers. Some TOX technologies have fuel costs 5-10x higher than other systems. A Thermal Oxidizer with a low initial cost could have a higher TCO over two years compared to that of a Catalytic Oxidizer or Regenerative Thermal Oxidizer.
Kono Kogs is happy to provide a cost-benefit analysis for your project. We’ll compare multiple technologies, explain the trade-offs of each option, and give you our professional recommendation on the most cost-effective system.
Questions to Ask when Considering a Thermal Oxidizer (TOX)
- Is a thermal oxidizer the most cost-effective oxidizer solution for my airstream? (See: Selecting an Oxidizer)
- Would a heat exchanger be cost effective?
- Is a plate heat exchanger or shell and tube style heat exchanger a better choice?
- Note: Shell and tube heat exchangers are more robust than plate style heat exchangers.
- Is there a potential for particulates that could plug the heat exchanger?
- Note: Shell and tube style heat exchangers are more robust better than plate style heat exchangers.
- Note: For Silicone application: Clean-able heat exchangers are usually the best solution.
- Note: Tube size is an important consideration when particulates are expected.
Other Considerations:
- Is there a need for heat or steam in your plant?
- Note: Secondary heat recovery has good payback with thermal oxidizers.
- Do local codes require low NOX operation?
- Note: Low NOX burners can be retrofit for these applications.
Thermal Oxidizer Manufacturers
The best-built Thermal Oxidizers make the best refurbished Thermal Oxidizers. Kono Kogs selects only the best pre-owned Thermal Oxidizers and stands behind them.
Check out our inventory of oxidizer systems from OEMs such as:
- CECO ADWEST Technologies
- Dürr MEGTEC Systems
- CMM Group
- REECO (Dürr)
- TANN Corp.
Kono Kogs Knows Everything About Thermal Oxidizers
Kono Kogs is the world’s leading supplier of refurbished Thermal Oxidizers. We also offer thermal oxidizer services including turnkey installation, repair, preventive maintenance, and upgrades. Our team has over 150 years of combined experience, and a 100% success rate in meeting performance guarantees. Whether we can help you get more years out of your existing system or find a replacement, we look forward to the challenge!
Frequently Asked Questions about Thermal Oxidizers
Find quick answers to more commonly asked questions about thermal oxidizers
Thermal Oxidizers (TOX) have a heat recovery (efficiency) of 70% typically, but some custom designs will use lower efficiency heat echangers if VOC concentrations are elevated. This technology has higher operating cost than most oxidizer systems.
TOXs typically operate at 1400o – 1500o Fahrenheit depending upon the VOC characteristics. Thermocouples inside the chamber monitor temperature and adjust gas burner firing as needed. Adequate temperature is essential to ensure VOC destruction efficiency. In most cases a data log of chamber temperature is required for air quality compliance.
Fairly clean process airstreams with low to medium air flow, and medium to high VOC concentrations (>10% LFL). TOX systems can be custom designed to handle high VOC concentrations as compared to CATOX and RTO systems. Typical applications are petrochemical, and chemical airstreams. Special applications are best served by TOX, such as silicone containing airstreams, or processes where secondary heat recovery allows the TOX to operate as efficiently as RTO systems or CATOAX systems because of the heat returned to the process.
TOX typically have a 0.5 second to 1.0 second dwell time for most applications.
VOCs must combine with oxygen and heat to trigger the chemical reaction that breaks them down into CO2 and H2O. There are many successful thermal oxidizer designs that ensure sufficient turbulence, such as introducing the process air at an angle to induce spin or creating internal choke points. The better the mixing and heat distribution, the higher the VOC destruction.
Catalyst utilized in a regenerative catalytic oxidizer (RCO) allows chemical reactions to occur at lower temperatures (700-800F) than they occur in a thermal oxidizer (typical 1400-1450F) or an RTO (typical 1600F).
Yes we can come out and help to determine what the problem is. Whether it be switching valves leaking; a leaking heat exchanger; poor air flow distribution; or poor catalyst performance. We can do a thorough evaluation and provide a turnkey solution in a short period of time and help to keep you in operation. If your system is a regenerative thermal oxidizer (RTO) see this blog post about stack test failures for more details on troubleshooting your RTO and test method.
An RCO is essentially an RTO with a catalyst layer added. (See What is an RTO?).
Emergency DFTO Thermal Oxidizer Fabrication for Recycling Emissions
An oil recycling company in the Southwest needed a new thermal oxidizer shell ASAP. This case study shows how KKI came through despite supply chain challenges.
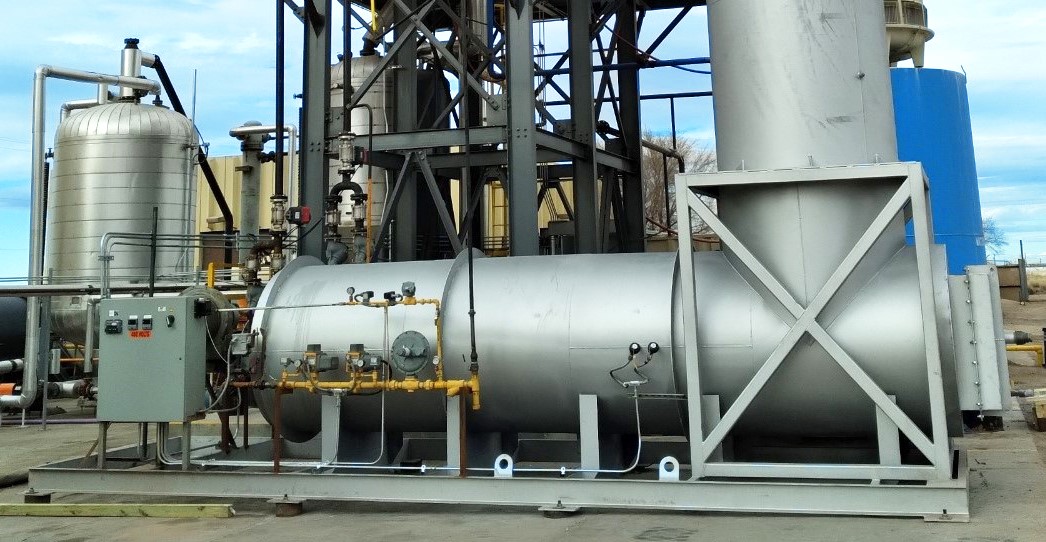
Kono Kogs is the world’s leading supplier of used thermal oxidizers.