RTO Installation & Ductwork Treating Flexographic Printing Emissions
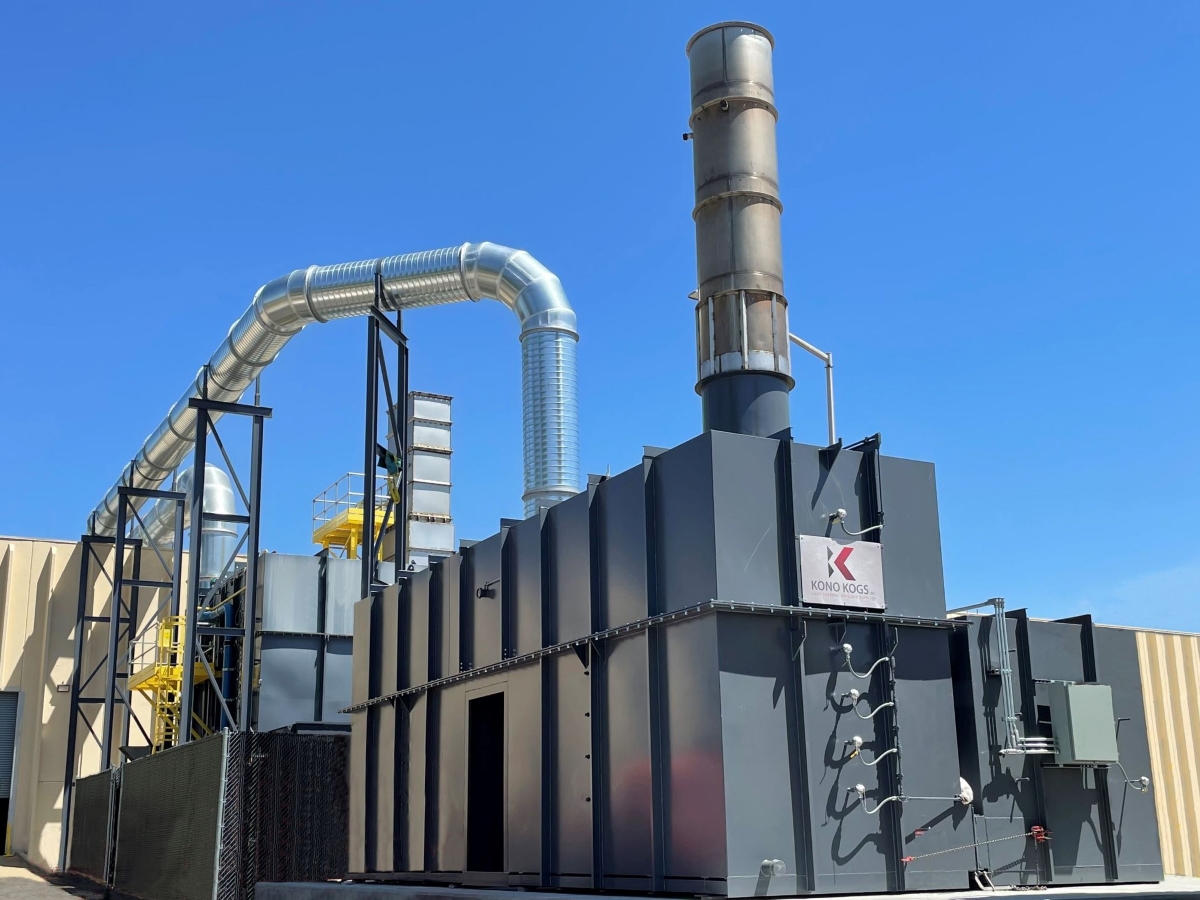
Kono Kogs refurbished & installed a second refurbished regenerative thermal oxidizer (RTO) for this major flexographic printer
Problem
A printer of food packaging utilizing flexographic printing presses was adding production capacity to serve their growing market share. Flexographic emissions include alcohols and acetates in their emission airstream. Standard RTO designs can provide 98-99% VOC destruction with ease, and RTOs in this application can have long life if designed properly.
Photos: In Progess
Click on a picture to enlarge
Solution
Kono Kogs provided a refurbished regenerative thermal oxidizer that had been previously treating emissions from a heatset web offset printing application. The design had a close-coupled poppet valve and ceramic media/combustion chamber which provided a small, space-saving footprint. Either a poppet or rotary switching valve would be a good fit for this application. The poppet design offered the most economical solution. The ceramic media bed design was reviewed and it was determined that a structured ceramic media bed was the highest performance option- it offered 95% thermal effectiveness with low fan horsepower. Air speeds through the beds were in the mid-range of the ceramic media suppliers design specs. This provides the highest thermal efficiency, optimal pressure drop, and long bed life.
Since a flexographic application is easily treated, some OEMs will look to cut design corners on their new systems to remain competitive with other OEMs. The untrained eye will not ask the necessary questions, nor understand the long term impact of the bed design provided by the OEM. Asking the right questions in the proposal review process, an end user can save themselves significant utility and maintenance costs over the decades-long life of their RTO. OEM’s that push a bed design to its limits certainly can reduce the upfront cost of the ceramic media, ceramic media supports, and insulation. An unsuspecting owner will spend significantly more in operating costs AND maintenance costs compared to a system designed with a normal safety factor. Asking critical questions is your key to making informed decisions. Click here for a guide to to the RTO evaluation/selection process.
Equipment & Services Provided
- Fully refurbished RTO (poppet
- Mechanical assembly of RTO at customer
- Fab & install process ductwork & supports
- Equipment and crew to install RTO and ductwork
- Equipment commissioning
- Parts Warranty & VOC destruction warranty
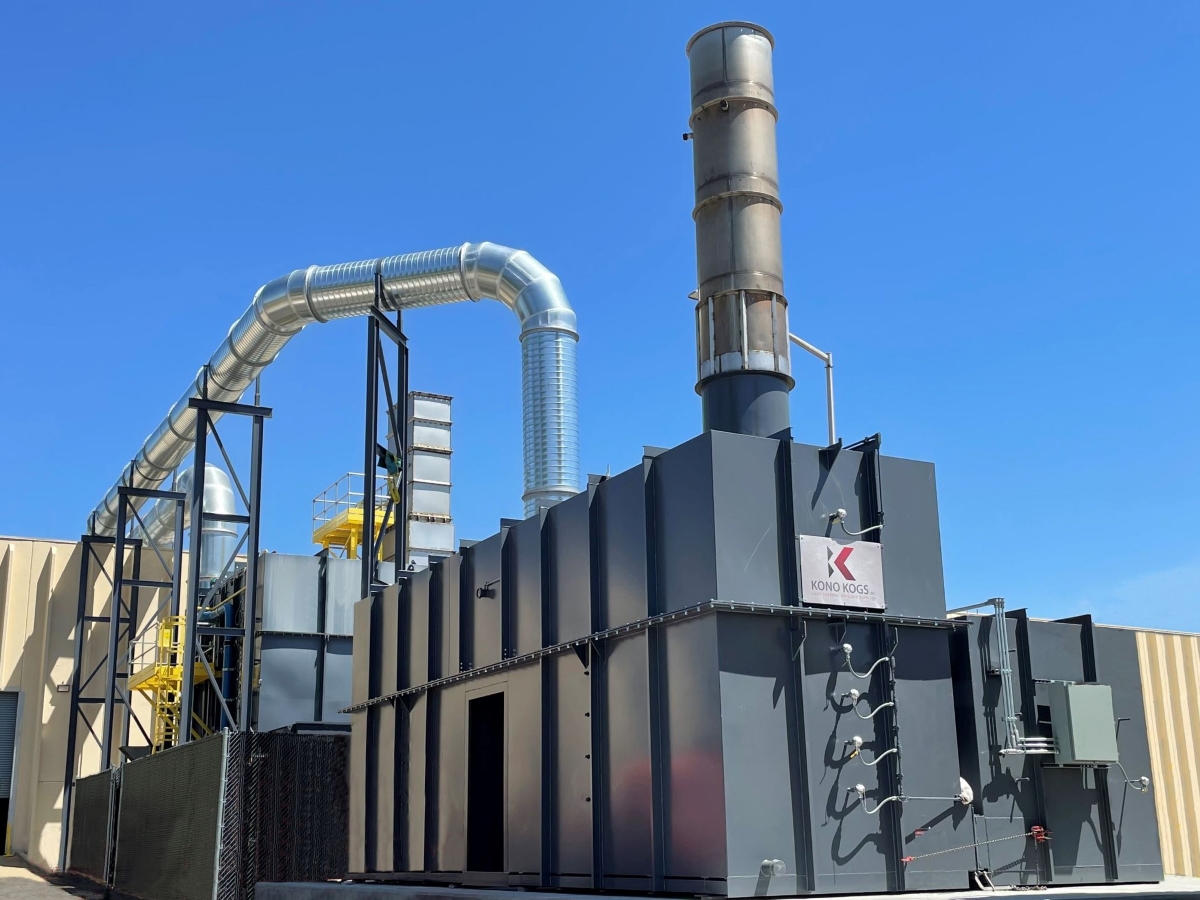
Results
Refurbished Poppet Valve RTO with structured ceramic media
Equipment:
- Refurbished RTO - 25,000 scfm
- Ductwork design with cross-over duct supports
Services:
- Mechanical Installation
- Ductwork including installation
- Equipment commissioning
Benefits: Lower Capital Cost and Low Maintenance
- RTO capital cost <60% of new equipment
- Parts & performance warranty matching new equipment
- Structured ceramic media beds
- Air speeds matching highest quality OEMs RTO design
- 10% fuel and electric savings compare to many OEM bed designs
- Slower airspeeds through beds than many new OEM RTOs
Low airspeeds provide:
- higher performance
- longer bed life
- longer RTO life
- lower maintenance
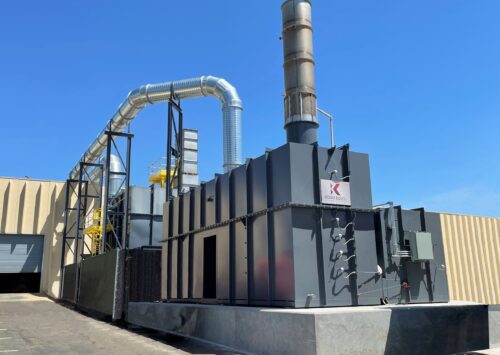
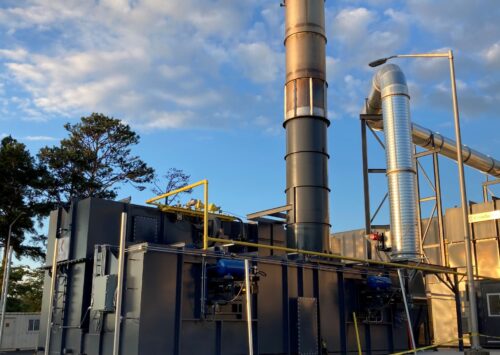
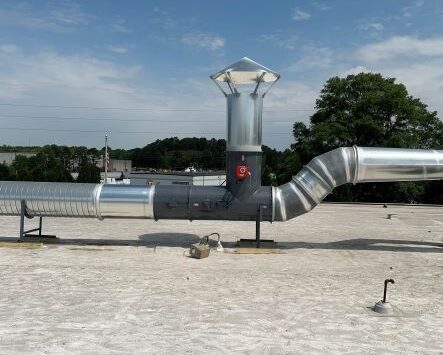
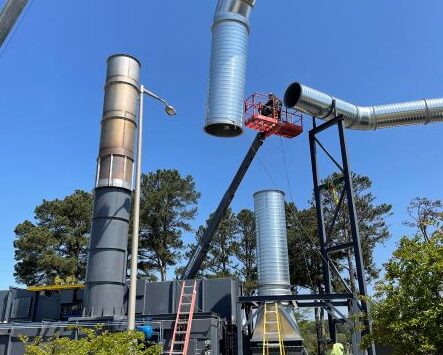
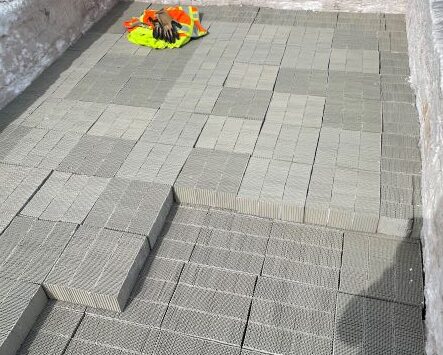
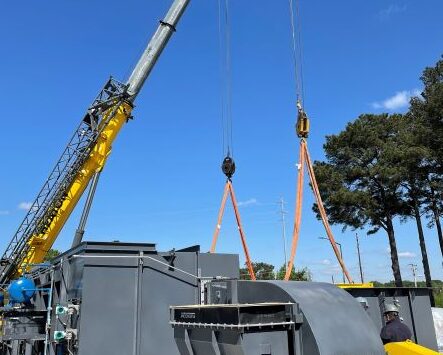
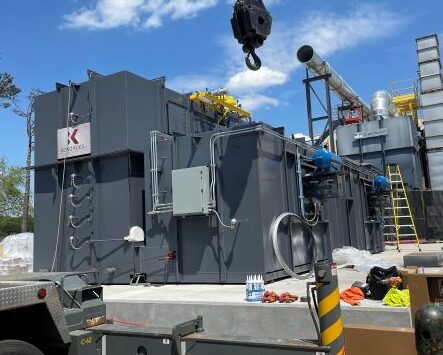