RTO Insulation, Damper and Duct Repair
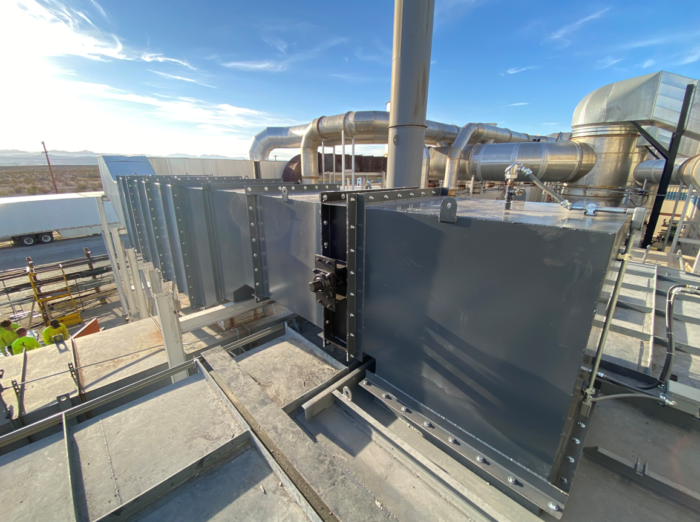
A Fortune 500 customer needed to replace a locked-up hot-side bypass damper and related ductwork along with repairing an insulated roof section on their large RTO.
Problem
A Fortune 500 customer needed to replace a locked-up hot-side bypass damper and related ductwork, and also repair an insulated roof section on their large regenerative thermal oxidizer (RTO). This operation runs 24/7/365 so proper planning and coordination with the production schedule were critical to keep downtime to a minimum.
Hot-side bypass dampers see extreme heat in RTOs and even the best-built dampers will fail eventually. They should achieve at least a 5-year life, and depending on the conditions and prevailing open/close position, a decade of performance is possible. The most typical failure is sag of the main damper shaft caused by extreme temperatures, the weight of the damper blade, and time. The sag requires increasing torque to turn the damper until eventually the actuator cannot overcome the torque.
Hot spots are usually due to voids/gaps in the insulation that allow hot air (1600°F+) to reach the outer wall of the duct. Gaps can be caused by improperly installed insulation modules, or from air leaks through poorly gasketed flanges or weld gaps/holes.
Hot spots are not uncommon and many times are not immediate problems. However, hot spots due to air leaks can quickly progress from small issues to major problems. Most RTOs operate under a positive pressure so any air leaks will pass hot air (1500°-1660°F) to the outside and begin to weaken and degrade the metal as it passes through the hole. The metal wastes away slowly but sometimes quickly, and as the hole increases in size the rate of damage increases exponentially. Air leaks are not only dangerous to equipment health, they pose a danger to personnel from hot air leaking out at pressure.
Solution
Kono Kogs was hired to remove and replace the hot bypass damper, related (insulated) ductwork, and cut out the compromised roof section and replace it with new metal. The new roof was installed, internally insulated and integrated with the existing uncompromised roof metal and insulation. We also properly re-packed the insulation to prevent hot spots. With proper coordination this repair was completed and the RTO was operational again in under 72 hours. Kono Kogs left an extremely clean job site, and also re-started and confirmed proper RTO operation prior to leaving.
Kono Kogs has experience refurbishing nearly every major RTO model on the market, even obsolete models from OEMs that are no longer in business.
We provide every component or service related to regenerative thermal oxidizers including relocation, trade-in, field repairs, field rebuilds/upgrades, emergency service, preventive maintenance service, and replacement with our refurbished, warrantied long-life RTO systems. We have hundreds of refurbished oxidizer units installed worldwide. Why buy new when you can buy better!

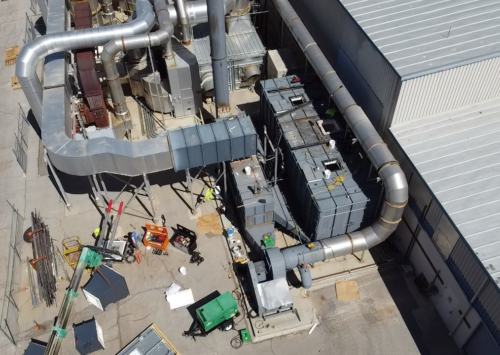
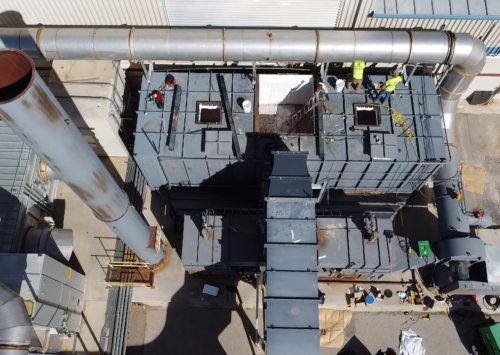
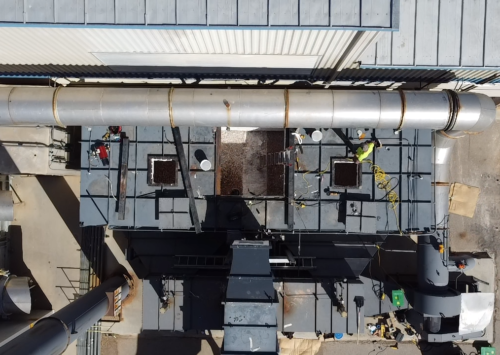
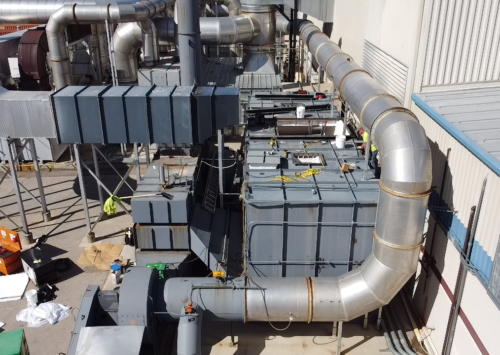
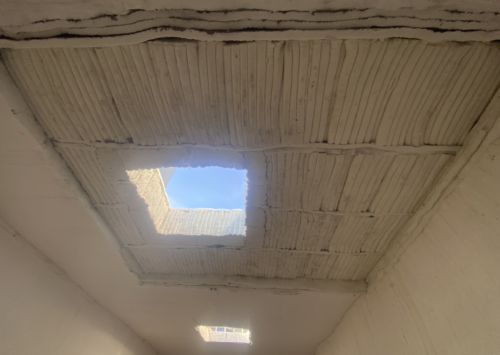
Equipment & Services Provided
- Inspect RTO and assess repairs needed
- Provide new hot-side bypass damper
- Fabricate and provide new internally insulated ductwork
- Provide repair plan, schedule work, & provide all materials
- Equipment and crew
- Thoroughly clean work site before leaving
- Equipment re-start
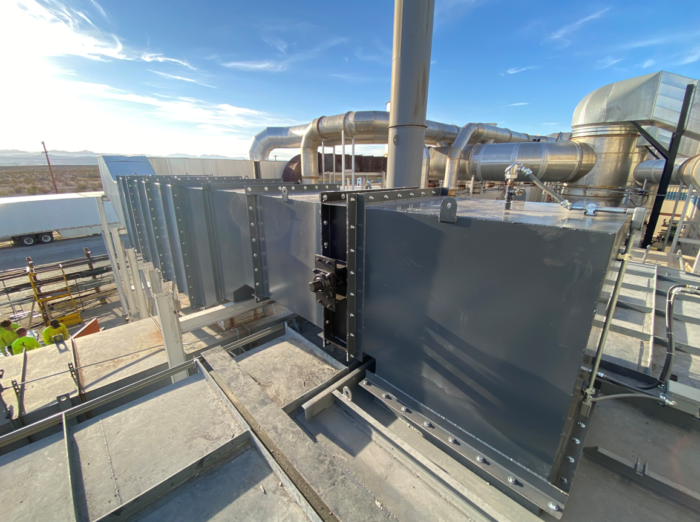
Progress Photos
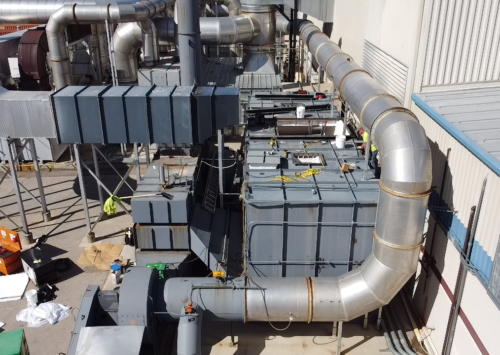