Selecting a Cost-Effective Oxidizer
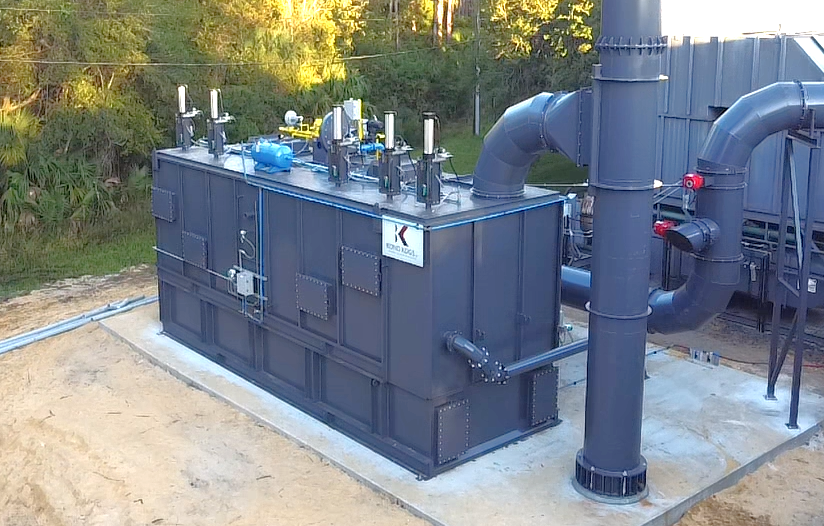
Tips to Control Thermal Oxidizer Costs
Selecting the appropriate air pollution control equipment for a particular industry can be challenging to say the least. Though companies are experts in their field, they are usually not experts in regard to air pollution control equipment. That’s where Kono Kogs comes in...
Our staff has over 150 years of combined experience applying, designing, installing and reconditioning thermal oxidizer systems, including:
- Regenerative thermal oxidizers
- Recuperative thermal oxidizers
- Catalytic oxidizers
- Pretreatment: Electrostatic precipitators & Baghouses
Thermal oxidizers are a major investment that does not have to turn into a major long-term expense. Proper selection of a technology for a particular application is the first step. In many cases, either a thermal oxidizer, catalytic oxidizer, or regenerative thermal oxidizer will meet the most important criteria: field-proven performance. If all designs will provide the performance required, and have historically performed well in the field, the next step should be quantifying the total cost of owning each applicable technology. Many applications can incorporate either catalytic oxidizer or thermal oxidizer technologies. However, one may break the bank and the other may not. Before selecting a pollution control technology, it is important to understand the total cost of ownership.
Regenerative thermal oxidizers have a heat recovery (efficiency) of 95% typically. This technology has the lowest operating cost of all thermal oxidizer systems – not to mention the longest service life and highest reliability. It’s even possible for an RTO to operate with no auxiliary fuel use whatsoever if process VOC concentration levels are >3-4% lower flammability limit (LFL).
It depends on numerous factors. See Selecting an Oxidizer for guidance or call us for guidance.
Up to 99% VOC destruction efficiency; and up to 97+% thermal efficiency.
How Thermal Oxidizer Operating Costs Affect Total Cost of Ownership
Kono Kogs recommends a thorough investigation of the Total Cost of Ownership (TCO) of an oxidizer before selecting a system. A system that is inexpensive to purchase may not offer the lowest TCO when looking out 1 or more years. For comparison of thermal oxidizer (or catalytic oxidizer) options consider using a minimum two-year time period to compare the TCO of the systems being considered.
LEARN MORE: Try our budget calculator
Cost factors for operating oxidizers
Cost of ownership includes:
- Initial investment – capital cost in the equipment purchase
- Operating costs – fuel and electricity expenditures
- Maintenance costs – part replacement & repair expenses and frequency
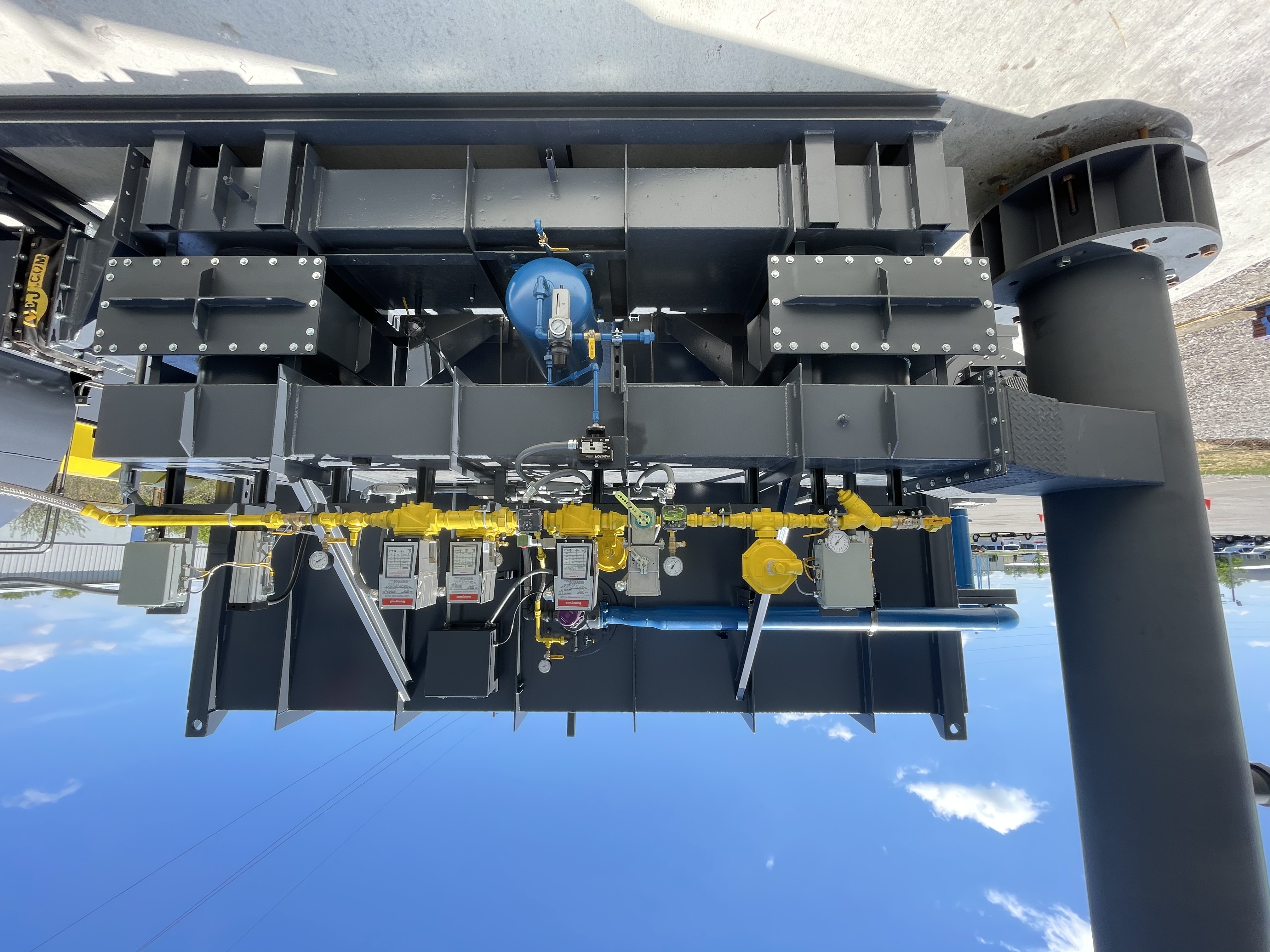
Capital Cost of the Equipment
- Equipment
- Shipping
- Installation
- Equipment Commissioning (start-up)
Operating Costs
- Fuel
- Electricity
- Compressed Air
Equipment Cost: How much does a thermal oxidizer cost? $35-$70/SCFM of air treated
For Example: An 8,000 scfm thermal oxidizer could cost $ 400,000
There are economies of scale for larger systems, but heat exchanger material, heat exchanger efficiency, and special construction can all drive the cost up significantly.
Operating costs can make even the least expensive thermal or catalytic oxidizer a poor investment. A system with low capital cost could have such a high operating cost that the total investment of ownership is 3-10 times more than a piece of equipment with a higher initial capital cost; usually due to the operating cost differences between systems. Some thermal oxidizer technologies require 5-10 times the fuel demand of other systems. For example, thermal oxidizer systems with 70-75% thermally effective heat exchangers may require 5-10 times the operating costs of a catalytic oxidizer or regenerative thermal oxidizer system. While the thermal oxidizer may have a lower initial cost, over a two-year span TCO of the thermal oxidizer can be 3-4 times that of a catalytic oxidizer or regenerative oxidizer.
How to Minimize Maintenance Costs
While maintenance costs are not a large percentage of the cost of ownership, it is important to understand the limitations of each oxidizer technology. The maintenance cost of owning an oxidizer is not difficult to quantify if the thermal oxidizer or catalytic oxidizer that is being considered has a proven track record in your industrial application.
Normal oxidizer maintenance consists of greasing bearings, replacing gasket, fan belts, and filters, which are relatively low cost. Catalytic oxidizer systems risk contamination of the catalyst and catalyst replacement can be very expensive. Also, regenerative thermal oxidizer and catalytic oxidizer systems risk plugging of their beds with solids, such as paint solids. This usually requires a complete replacement of the ceramic media in an RTO, which is expensive; or requires wash down of the media beds, which requires downtime.
On-going maintenance costs will only be fractionally different across well-built oxidizer designs; however reliability issues and poor support common with some lower cost designs/OEMs can skyrocket your maintenance cost, especially when lost production is considered.
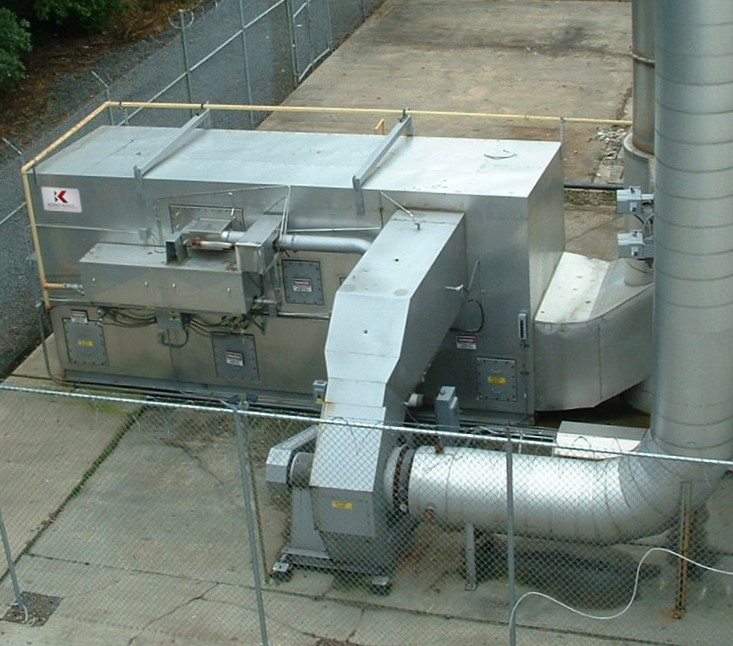
While each of these technologies are proven performers in many industries, due diligence is necessary to ensure that the thermal, regenerative thermal oxidizer or catalytic oxidizer being considered has been proven in your industrial application. A supplier of air pollution control equipment should be able to provide references in industries where their equipment has been proven, or where a specific technology (catalytic oxidizers, thermal oxidizers or regenerative thermal oxidizers) has been performing well for at least one year.
Further Reading:
- EPA’s cost reports and guidance for Air Pollution Regulations
- Incinerators & Oxidizers Calculation Spreadsheet (.xlsm Download)
Know Your Airstream for Optimal Cost Efficiency
To select the proper technology, it is important to understand how each system destroys volatile organic compounds (VOC). Depending on your specific need, our team may recommend one of three types of systems:
- A thermal oxidizer destroys hazardous, toxic chemical waste by oxidizing (breaking the bonds of the hydrocarbon), at high temperature, the emissions contained in a waste airstream.
- Regenerative thermal oxidizers (RTOs) destroy VOCs in the same way but utilize the highly energy-efficient technology of regenerative heat exchange
- Catalytic oxidizers destroy VOCs in the same way as RTOs, but the presence of catalyst allows the destruction to occur at a lower temperature (usually 600-650F).
The goal is to heat the VOCs to the reacting temperature but to achieve this, the entire airstream must be heated to the reaction temperature. This is an important consideration, especially for spray booth applications, which tend to draw a large quantity of air, but only have a small concentration of VOCs. If the amount of air that is exhausted to a thermal oxidizer can be reduced, the size and cost of the oxidizer and the operating (fuel and electric) costs can be reduced, sometimes significantly.
Factoring in Fuel Costs
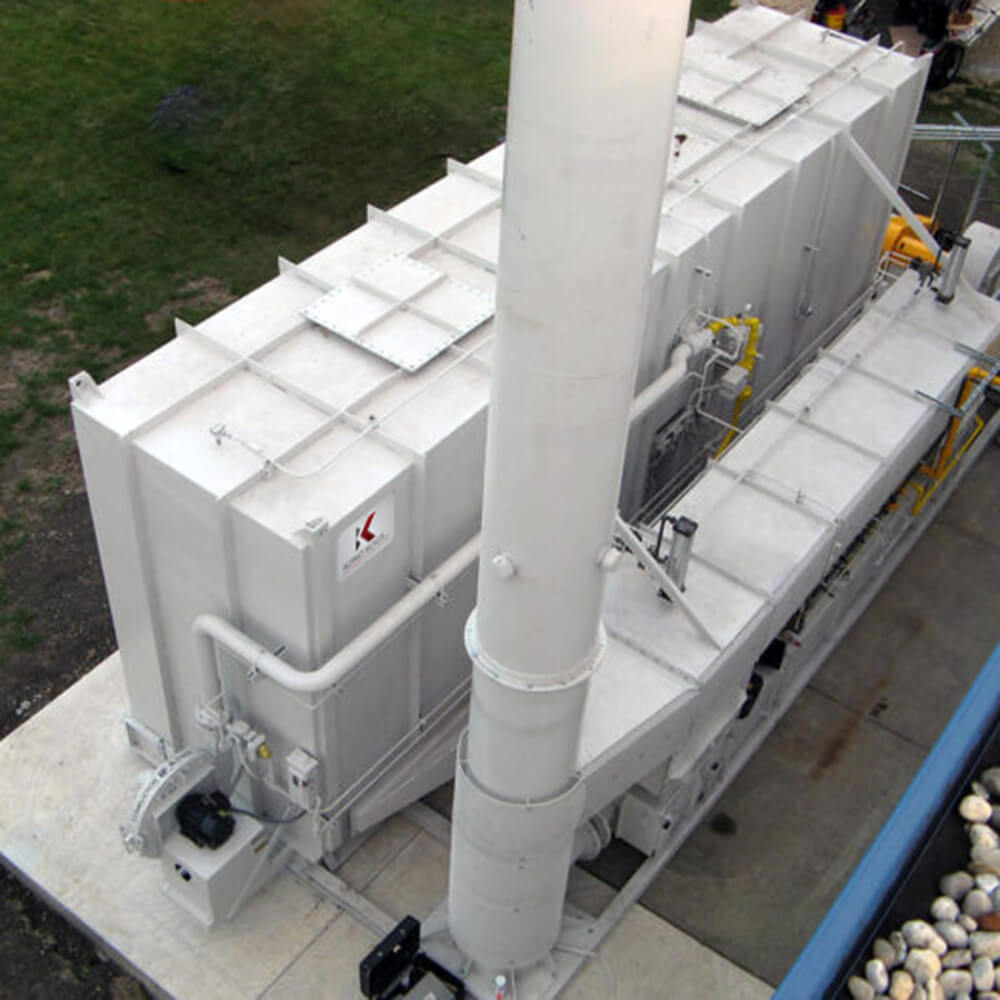
Recuperative thermal oxidizer systems provide high VOC destruction efficiency, but are very costly to operate due to the high operating temperature (1400F) and low thermal efficiency of this design. These systems are rarely used except in special applications. The fuel usage can be 5-6 times that of a comparable catalytic oxidizer and 7-10 times the cost of operating a regenerative thermal oxidizer. A thermal oxidizer utilizes a burner and a heat exchanger to heat the contaminated airstream and break the hydrocarbon bonds, recombining the carbon, hydrogen and oxygen (oxidizing) to produce water vapor and carbon dioxide.
Regenerative thermal oxidizer systems (RTOs) also destroy VOCs and fumes by oxidizing the emissions at high temperature. The difference between the regenerative thermal oxidizer and thermal oxidizer are, most importantly, the thermal efficiency. A regenerative thermal oxidizer has a nominal 95% thermal effective heat exchanger. The conventional thermal oxidizer has a nominal 70% effective heat exchanger. In the most simplified terms, the regenerative oxidizer will lose 5% of its energy input (fuel) up the exhaust stack (100%-95%= 5%). The thermal recuperative oxidizer will lose 30%.
The simplified comparison shows that, on average, a regenerative oxidizer will use 1/6th (5% divided by 30%) the fuel of a thermal oxidizer. Regenerative thermal oxidizers also have one other limitation that is not an issue with recuperative thermal oxidizers or catalytic oxidizers.
Lower Fuel Costs in VOC Destruction
Destruction of pollutants gives off heat (exothermic reaction). This heat offsets the amount of fuel needed to heat the pollutant airstream. In some conditions, the number of pollutants will be high enough that the oxidizer can operate fuel free (no fuel usage). This is a good indication of the thermal efficiency of an oxidizer. A recuperative thermal oxidizer with a 70% effective heat exchanger will operate fuel-free at solvent concentrations of 20% LEL or greater. A regenerative thermal oxidizer will operate fuel free at as low as 4% LEL.
For many applications, catalytic oxidizer systems accomplish the same VOC destruction performance as a thermal oxidizer system, at lower temperature and therefore lower fuel costs. Catalytic oxidizers are relatively energy-efficient with low operating costs and they do not cause extreme thermal stress to equipment because they operate at a low temperature. Most catalytic oxidizers operate at 650F or less. This lower temperature combined with a 70-75% heat exchanger effectiveness allow catalytic oxidizers to operate fuel-free at emission concentrations of 8% LEL or greater.
Fuel Requirements: RTOs vs. Catalytic Oxidizers vs. Recuperative Thermal Oxidizers
In general, catalytic oxidizer systems require about 20% of the fuel used by a recuperative thermal oxidizer. And, regenerative thermal oxidizers (RTOs) require only 60% of the fuel used by a catalytic oxidizer. RTOs are the system of choice for most applications because of their reliability and low operating costs. At low flow rates the difference in fuel cost is not significant between a catalytic oxidizer and a regenerative thermal oxidizer, but as flow increases above 7,000 scfm the fuel cost differences can become significant.
Flow Resistance Affects Electric Costs
Since some regenerative thermal oxidizers have higher flow resistance (pressure drop across the oxidizer) than catalytic and recuperative thermal oxidizers, the fan power required to force air through (or draw it through) the oxidizer can be higher than what’s required for catalytic thermal recuperative systems, resulting in higher electric costs. However, structured ceramic media has become more common as prices drop. Most modern RTO designs achieve very low electric operating costs by using structured media. While structured media can’t be used for some particulate-laden streams, most RTO applications offer excellent payback for the added upfront cost.
So, for high airflows and light VOC concentrations, the regenerative thermal oxidizer still provides significantly lower overall operating costs than catalytic or recuperative thermal oxidizer systems because of the RTOs fuel efficiency. In fact, a recuperative thermal oxidizer will likely always be more expensive to operate than a regenerative thermal oxidizer.
Other Considerations: RTO Design Limitations & Puff Capture Retrofit Options
Most regenerative systems use a two chamber design, typically allowing over 98% VOC destruction. The energy efficiency of the RTO is a result of its flow-reversing design. This reversal of flow that occurs (about every 3 minutes) causes a puff of dirty air to exit the exhaust stack. When the flow control valves switch position, a small portion of the contaminated air becomes trapped momentarily, then is back-flushed out to the exhaust stack. With visible emissions, such as heavy condensables or long-chain hydrocarbons, the back-flushed air will be visible as it exits the oxidizer exhaust stack. As a rule of thumb, if the process exhausting to the RTO has a visible exhaust, it will have a visible puff during every valve switch. While the oxidizer still maintains an overall 98+% VOC destruction efficiency, the puff can be a nuisance issue if a facility is near a residential area. Special options are available to capture this puff of emissions. This option is sometimes called puff capture or VOC entrapment. Kono Kogs has retrofit systems with this option, and many new RTOs are being configured with this feature as well.
Current Trends Affecting Thermal Oxidizer Cost
RTOs are by far the technology of choice for most applications today because they offer high VOC destruction rates, reliability, and fuel efficiency. Poppet valve designs have been proven over the 25 years they have been used for RTO systems. Some designs over-complicate the poppet valve and should be avoided or added maintenance downtime should be planned into your production schedule.
Another switching valve technology is a rotary valve RTO. These have been around for over 15 years and a few of them have proven reliable. They can be maintenance challenges in certain applications, and certain systems are more maintenance-intensive due to the bed separation method plus the high heat location of the bearing for rotation. Rotary valve technology has evolved to where these valves are proven and reliable performers. Utilizing electric drives (motor, VSD) in cold weather locations addresses pneumatic freezing issues common in cold weather RTO switching valves.
Originally designed for high airflow rates with low VOC concentrations, recent advances in regenerative thermal oxidizer (RTO) systems allow economical control of small emission airstreams (<3000 scfm) as well. Advancements in structured ceramic media and its lower cost have allowed RTO systems to operate at horsepowers rivaling catalytic systems and sometimes lower. And structured ceramic media prices now allow fast payback over random packed media systems.
A guide for selection of a regenerative thermal oxidizer can be found here: How to Purchase a Regenerative Thermal Oxidizer.
Get a Free Cost Estimate & Valuable Insights
The air pollution equipment technology that is appropriate for a given application depends on the type and volume of emissions produced by the industrial process. Kono Kogs specializes in helping companies determine which air pollution control equipment will best destroy their emissions at an affordable total cost of ownership. Kono Kogs can provide Total Cost of Ownership (TCO) estimates for any system we offer, helping you make the most informed choice of oxidizer options available.
Give us a call and we can help you with your oxidizer selection process, even if we don’t have a system that matches your needs. Or, maybe we have a great match for you in our inventory. We look forward to the opportunity to help you navigate this potentially confusing process of selecting an emission control system for your facility/client.
Contact our team with your questions or request a quote today!
RTO Installation & Ductwork Treating Flexographic Printing Emissions
Kono Kogs refurbished & installed a second refurbished regenerative thermal oxidizer (RTO) for this major flexographic printer
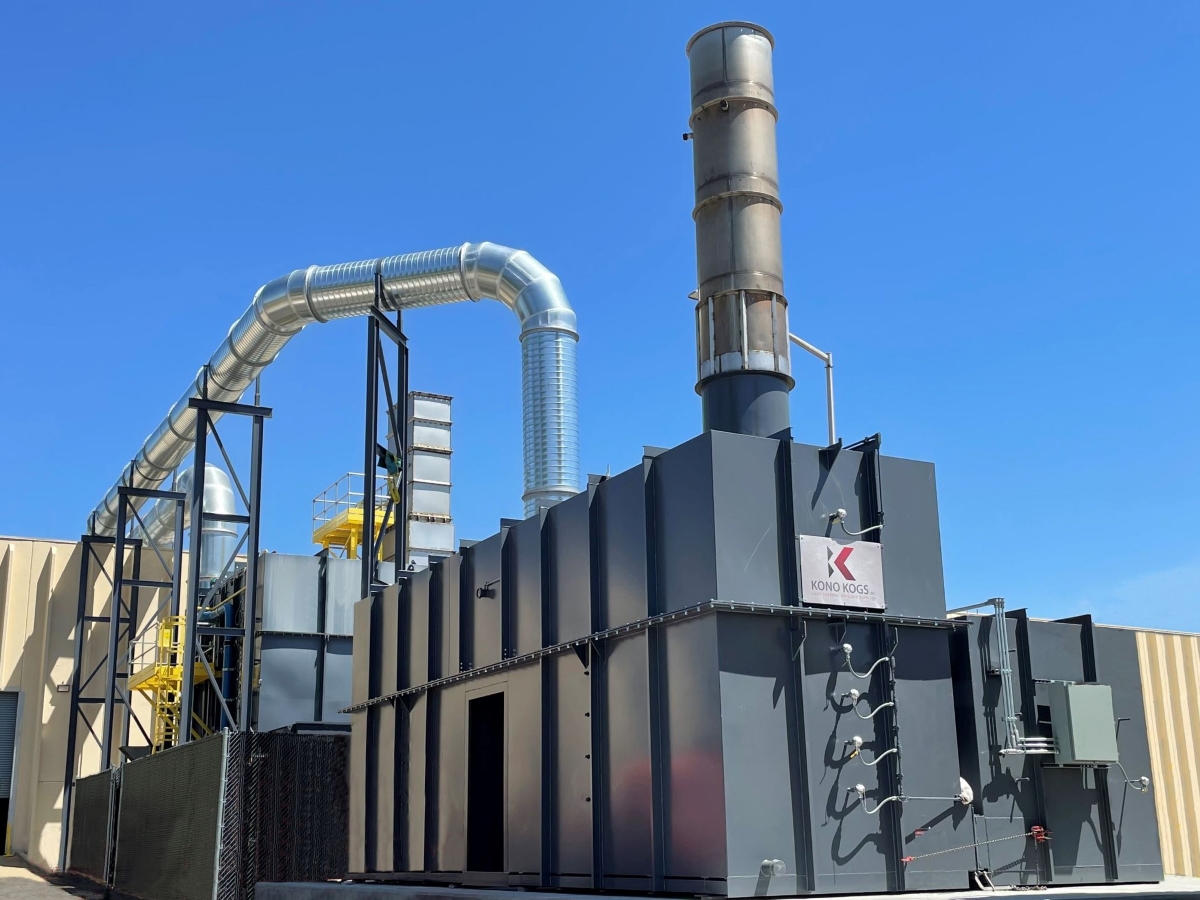