Regenerative Thermal Oxidizer vs. Standard Thermal Oxidizer
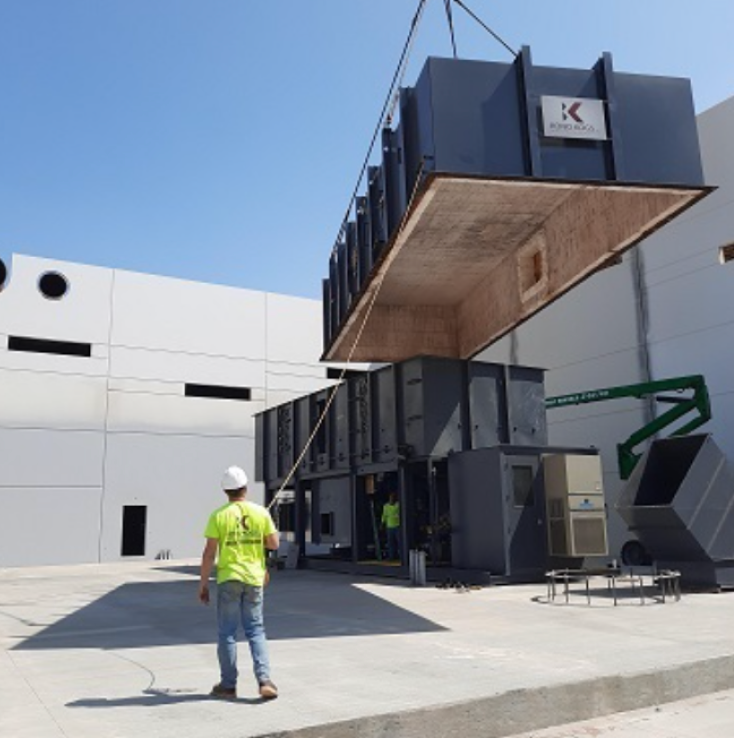
What are the Differences Between an RTO and a Thermal Oxidizer?
The difference between a Regenerative Thermal Oxidizer (RTO) and Recuperative Thermal Oxidizer (TOX) is the method of heat recovery; one utilizes multi-direction regenerative heat exchange, and the other a single direction conventional heat exchange. Both systems are thermal oxidizers, achieving destruction of air-borne pollutants (VOCs and HAPs) through heating the airstream to very high temperatures.
Different Types of Heat Exchangers
Both RTO systems and TOX systems incorporate a heat exchanger to recover heat from the airstream before it exits the oxidizer. The recovered heat is used to pre-heat the polluted air that is entering the system, to reduce operational cost (fuel). Once the air is preheated in the heat exchanger of either system type, a burner provides any additional heat needed to raise the airstream to the setpoint temperature.
TOX
A recuperative thermal oxidizer (TOX) has a conventional metal air-to-air heat exchanger to pre-heat the incoming dirty/polluted airstream. The heat exchanger is made of stainless steel or exotic metal and is either a plate type or a shell & tube design. The typical heat exchanger effectiveness is 70%.
RTO
A regenerative thermal oxidizer uses a ceramic heat exchanger to pre-heat the incoming dirty/polluted airstream. The heat exchanger is made of ceramic of various shapes and types that act as a heat sink. The typical heat exchanger effectiveness is 95%.
Air Flow Direction Differences
A TOX unit and an RTO have essential differences in the way they handle the air flow through the process.
TOX
In a thermal oxidizer (TOX) the polluted air passes air continually through the system with no airflow reversal. This is a conventional heat exchange most people are familiar with.
RTO
In a regenerative thermal oxidizer (RTO) the polluted air reverses airflow direction periodically. This achieves the regenerative heat exchange for extremely high (95%+) heat exchanger performance.
Visible Emissions
Standard TOX units operate with slightly higher VOC destruction efficiency than RTOs, which lends to differences in the visible emissions from each.
TOX
A TOX typically has no visible emissions during operation, with nearly all VOC types.
RTO
For most VOC types treated by an RTO, there will be no visible emissions during operation. However, certain long-chain hydrocarbon VOCs that condense in an airstream, could produce visible “puffs” whenever the RTO switches flow direction.
Dirty air that has not been fully treated in the RTO, combined with some incoming process emissions will exhaust briefly to the exhaust stack until the split-second valve switch completes. Though an RTO achieves 98+% VOC destruction even with these puffs, the optic of these puffs can be problematic for facilities near residential areas.
To alleviate this puff a special feature can be added to the RTO to capture and treat this puff, eliminating it. This feature is sometimes called a puff capture or might be called VOC entrapment. Visit here for more information on RTO operation and the cause of the puff.
Efficiency: RTO vs. TOX
The main advantage of an RTO is the significant fuel savings compared to the TOX. Regenerative heat exchange is significantly more efficient than a TOX, requiring approximately 20% of the fuel that a TOX would require.
TOX vs. RTO Characteristics
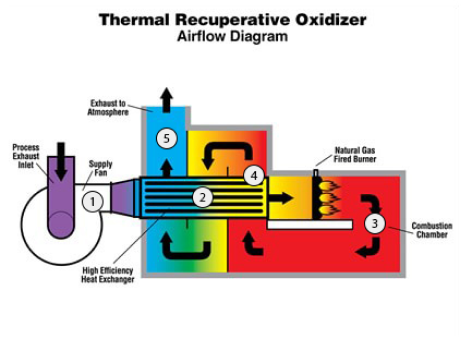
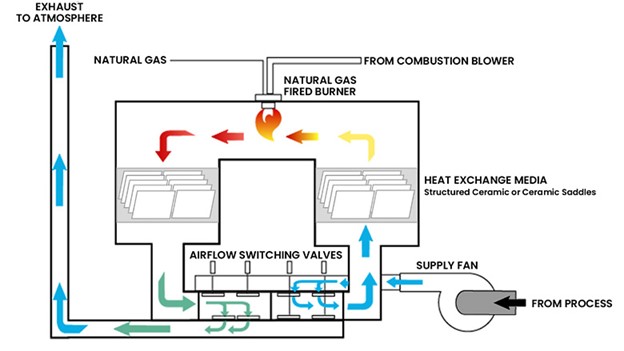
Regenerative Thermal Oxidizer (RTO) or Thermal Oxidizer (TOX) – Which is Better?
Thanks to their fuel efficiency, regenerative thermal oxidizers are the oxidizer technology of choice for most industrial air emission control applications. In addition to high VOC destruction and low operating cost, RTOs also have the longest life and the highest reliability when compared to other thermal oxidizer technologies. Even at low VOC concentrations, RTOs can operate at near-zero fuel consumption. Upfront capital costs for RTOs and TOXs are comparable. For all these reasons most industrial applications are best served by an RTO.
Four Exceptions when a TOX may be a better option than an RTO
Despite the ways that a regenerative thermal oxidizer may outperform a TOX for many applications, there are a few instances where a standard recuperative thermal oxidizer is the better choice.
When High VOC Destruction Efficiency is Required
For applications requiring extremely high VOC destruction efficiency, a TOX may be the only option.
When Additional Process Heat is Available
When heat can be returned back to aid in process heating through the use of a secondary heat exchanger, a TOX may offer comparable operating costs to an RTO.
When it's a Low Annual Run Time Application
Manufacturers with batch processes or processes that have very low annual run time may prefer a standard thermal oxidizer with no heat exchanger (Direct fired thermal oxidizer- DFTO) because of the low upfront capital cost. The fuel use will be extremely high (20X) for a DFTO vs. RTO, but for short run/batch applications it can make economic sense.
Note: TOX systems are not a good match for batch applications. The multiple heat-up/cool-down cycles that occur can fatigue the metal of the heat exchanger, shortening its life.
When There are High VOC Concentrations
For these applications an RTO may be too efficient and overheat, even with some special features such as hot gas bypass. Thermal oxidizers can overheat as well if the VOC concentration exceeds 25%-35% LFL. DFTOs and ground flares may be a better match for these applications.
Contact the thermal oxidizer experts at Kono Kogs for more information on key differences between available pollution abatement systems.
For more detailed comparison of oxidizer technologies, read tips about selecting an oxidizer.
Common Questions about RTOs and Thermal Oxidizers
Get quick answers to some of the FAQs around RTOs and TOX systems of pollution control
Regenerative thermal oxidizers (RTOs) have a heat recovery (efficiency) of 95% typically. This technology has the lowest operating cost of all thermal oxidizer systems – not to mention the longest service life and highest reliability. It’s even possible for an RTO to operate with no auxiliary fuel use whatsoever if process VOC concentration levels are >3-4% lower flammability limit (LFL).
Thermal Oxidizers (TOX) have a heat recovery (efficiency) of 70% typically, but some custom designs will use lower efficiency heat exchangers if VOC concentrations are elevated. This technology has higher operating cost than most oxidizer systems.
Yes, RTOs can be designed to match your specific exhaust airstream characteristics. They are typically optimized for airstreams with solvent concentrations in the 0–10% Lower Explosive Limit (LEL) range. For higher concentrations up to 25% LEL, additional features such as hot gas bypass systems may be needed to ensure safe and efficient operation.
Yes, if your process stream contains corrosive compounds or halogenated compounds (like chlorine, bromine, or fluorine), the RTO may require special materials of construction such as high-alloy stainless steels or corrosion-resistant coatings to ensure long-term durability and safe operation.
Regenerative thermal oxidizers (RTOs) typically have a 0.5 second to 1.0 second dwell time for most applications.
Typically 1400° F minimum up to 1550° F depending upon the VOC characteristics. Read more in Operating Temperatures of Different Oxidizers.