Regenerative Thermal Oxidizer Treating Chemical Process Emissions
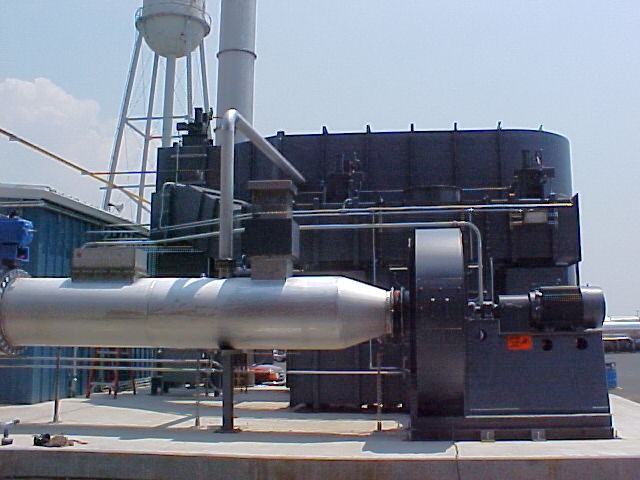
Case study: Batch chemical manufacturer required emission controls for a process expansion. We supplied a used RTO from our inventory with all necessary features.
Problem
Batch chemical manufacturer required emission controls as part of a process expansion in their New Jersey facility. Emissions from the new process would exceed their emission cap. They had purchased a new RTO at a sister facility 2 years ago and were having significant reliability issues with it. They wanted an RTO unit to handle the large swings in LEL from their multiple reactor vents, and needed to achieve 98% VOC destruction and potentially faced the potential of a 99% requirement. Each batch chemical reactor vent produced an exhaust stream with VOC concentrations that vary between 1% LEL to well over 100% LEL, some streams blanketed in nitrogen. A fan, dilution air system, and an LEL monitoring system were installed to maintain the LEL between 1% LEL and 15% LEL.
Photos: In Progess
Click on a picture to enlarge
Solution
A thermal recuperative oxidizer would have been a good fit for this application, but the operating costs at low LEL conditions would have been excessive. An RTO (regenerative thermal oxidizer) was another alternative, and it offered low cost of operation at low LEL levels. However, the LEL swings were a major consideration.
Kono Kogs analyzed the operating conditions and recommended an RTO which had several features that would provide either a heat sink and/or heat release for the high LEL spikes. The RTO, by design, has a large thermal mass. This allows the system to absorb the energy peaks generated by spikes in LEL. However, extended time at high LEL would create an over temperature condition, and shut down the RTO.
We had a used regenerative thermal oxidizer (RTO) available in our inventory with the necessary features. This system had a hot side heat exchanger bypass, which dumps energy directly to the exhaust stack, allowing the RTO to operate in LEL ranges from 1% to 20% LEL. We also incorporated a dilution air feature that modulated a supply of fresh air into the process stream to act as an additional heat sink. The combination of these features and the natural thermal stability of the RTO created a system that has performed well in this application.
Photos: After
Click on a picture to enlarge
Equipment & Services Provided
- Fully refurbished used Regenerative Thermal Oxidizer (RTO)
- Performance and parts warranty
- Low cost RTO at approximately half the cost of their previous RTO purchase.
- Experience controlling emissions with extreme LEL variations.
- Refurbished RTO (from an OEM R&D facility) had been idle for 2 years.
- Replacement ceramic media increased capacity by 25% with a change from a random packed (1″ saddle) ceramic heat exchange material to a structured ceramic material.
- Configured unit to add VOC entrapment (or puff capture) resulting in >99+% VOC destruction.
- Oxidizer PLC logic modified to interface with Process & LEL System
- Partnered with OEM to update PLC, operating program, and provide support for customer’s hazard analysis.
- Guaranteed 99% VOC DRE (actual >99% VOC DRE)
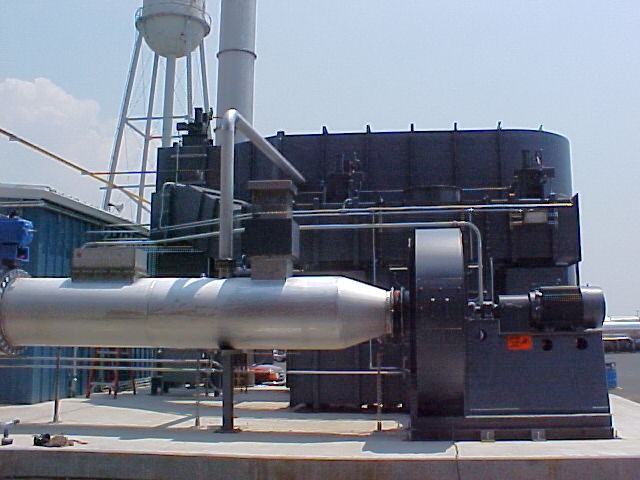
Results
The RTO met regulatory compliance (99% VOC DRE) and provided significant capital cost savings compared to new equipment. And operating cost savings were substantial compared to a thermal recuperative oxidizer.